物料管理程序
一、目的:为确保物料有效管理,合理控制耗损,特制订此物料管理程序。
二、范围:凡有关生产所需之原辅材料均属之。
三、权责:
3.1 物料请购:物控及各生产单位
3.2 物料采购:采购
3.3 物料领用:物料员
四、原物料备料流程图:
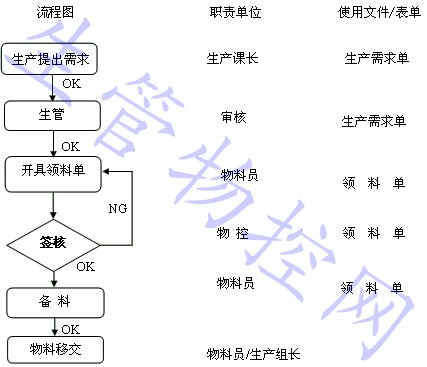
五、作业内容:
5.1 生产提前一天提出《MT-D-0012生产需求单》,并交于生管审查,生管审查完成后交于资材课以待备料。
5.2 物料员按照《MT-D-0012生产需求单》﹑《MT-D-0009订单追踪表》开具《MT-D-0003领料单》至物控处审查,确定OK后备料。
5.3 物料员将备好之物料移交生产单位组长,生产组长需进行数量的清点,并确实其物料数量准确性后签收。
5.4 移交签名时需注明移交时间,避免延误时间耽误生产。
六、原物料移交流程图:
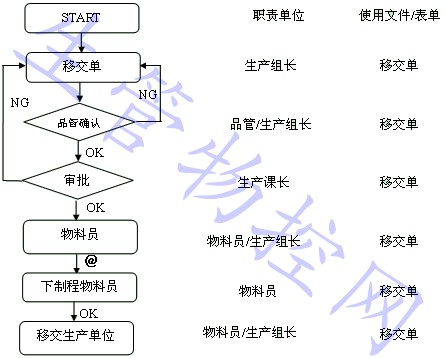
#p#副标题#e#
七、作业内容:
7.1 生产组长整理好物料后移交品管做品质认定再转生产课长审批。
7.2 品管确定OK后生产组长需将物料移交于本部之物料员,双方需核对其数量,待数量确定OK后在移交单上签名核实。
7.3 该部门之物料员需将物料移交下一制程之物料员,物料员之间需核实其数量,数量确定OK后进行物料移交。
7.4 下一制程之物料员将收到之物料再次移交到本生产单位,双方需核对数量,避免有数量上的争议,并签名核实。
7.5 移交签名时需注明移交时间,避免延误时间耽误生产。
八、成品入库作业流程图:
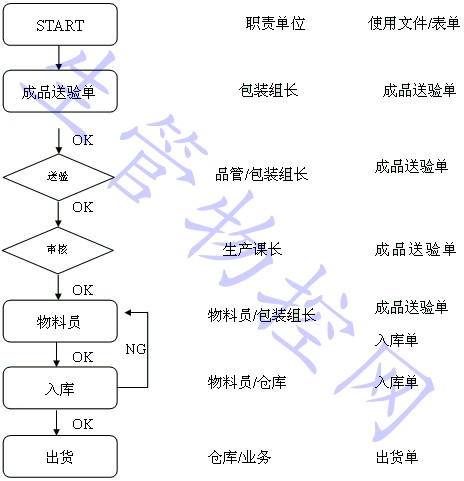
九、作业内容:
9.1 生产包装组长开送验收单交由品管验收,品管验收合格后交于本部门课长审核,并将送验单及成品移交物料员,双方确认其数量后由物料员开具《MT-D-0002入库单》。
9.2 物料员将《MT-D-0002入库单》移交到仓库,并与仓库做物料交接,仓库接到后端业务出货通知后安排出货。
十、生产退料作业流程图:
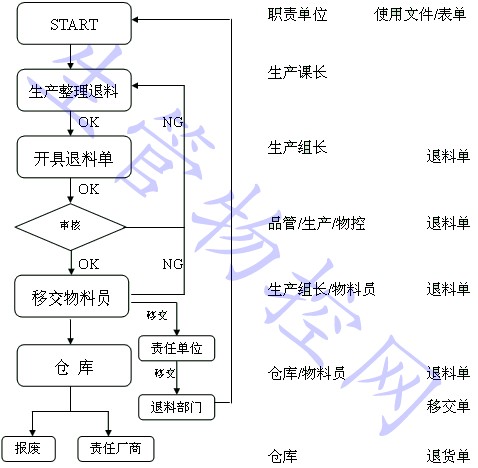
#p#副标题#e#
十一、作业内容:
11.1 生产单位将不良退料整理好后交于单位课长审批,再转品管确认其品质状况,以便退料。
11.2 品管需在退料单上注明其退料处理方式,区分其责任单位。
11.3 品管裁定可以返修的,物料将此物料退到该责任单位处理,责任单位再将返工后的物料移交退料单位。
11.4 退料单经品管认定后,再转交物控审查,让其了解退料状况。
11.5 生产单位将签核完后的退料单再移交物料人员,物料人员确定其数量后在退料单上签名,并将不良品移交仓库。
11.6 移交签名时需注明移交时间,避免延误补料时间。
十二、补料作业流程图:
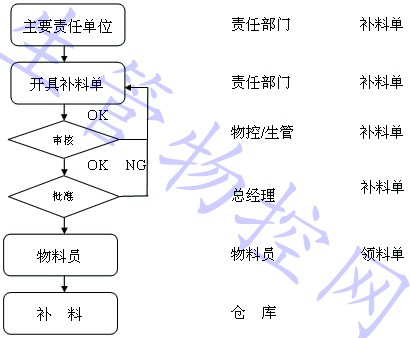
十三、作业内容:
13.1 由主要责任单位填写《MT-D-0006补料单》交由生管/物控人员审查,让其了解补料状况。
13.2 责任部门将生管/物控审查后的《MT-D-0006补料单》呈总经理审批。
13.3 责任部门将总经理审批后的《MT-D-0006补料单》移交物料员并要求补料。
13.4 仓库收到领补料单后发料。
十四、生产预补料:
由于偶尔会产生生产突发状况,导致物料用量不足之情况,此因素较多(eg:工程用量不够、损耗不够、或生产损耗偏高),如果到订单完成时才补料,会导致原物料购买压力大,且交期不容易达到要求,生产可根据自身实际状况预补料,以便生产顺利出货,其流程按补料流程执行!
十五、有关退补料相关规定说明:
15.1退料如有疑问,最终认定单位由工程裁示。
15.2 退料单与补料单一并开出才具有时效性。
15.3 排程的长单每周清一次退料。
15.4 短单每个P/O完成时需清理。
15.5 外发的订单每天都要清理退料,以便即时退补料。
15.6 退料时间生产每天11:00到品管单位,下午16:00-17:00为仓仓库接收退料时间。
十六、相关文件:无
十七、相关附件
17.1《MT-D-0002:入库单》
17.2《MT-D-0003:领料单》
17.3《MT-D-0004:退料单》
17.4《MT-D-0006:补料单》
17.5《MT-D-0012:生产需求单》
17.6《MT-D-0014:在制品移动交接单》
二、范围:凡有关生产所需之原辅材料均属之。
三、权责:
3.1 物料请购:物控及各生产单位
3.2 物料采购:采购
3.3 物料领用:物料员
四、原物料备料流程图:
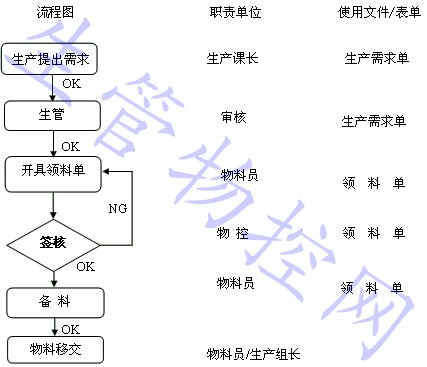
五、作业内容:
5.1 生产提前一天提出《MT-D-0012生产需求单》,并交于生管审查,生管审查完成后交于资材课以待备料。
5.2 物料员按照《MT-D-0012生产需求单》﹑《MT-D-0009订单追踪表》开具《MT-D-0003领料单》至物控处审查,确定OK后备料。
5.3 物料员将备好之物料移交生产单位组长,生产组长需进行数量的清点,并确实其物料数量准确性后签收。
5.4 移交签名时需注明移交时间,避免延误时间耽误生产。
六、原物料移交流程图:
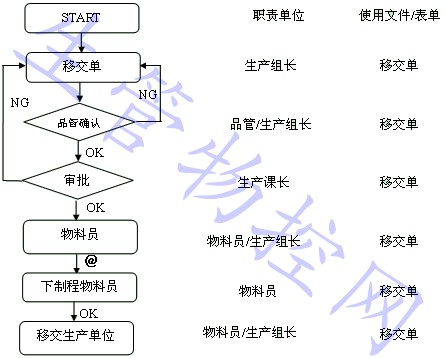
#p#副标题#e#
七、作业内容:
7.1 生产组长整理好物料后移交品管做品质认定再转生产课长审批。
7.2 品管确定OK后生产组长需将物料移交于本部之物料员,双方需核对其数量,待数量确定OK后在移交单上签名核实。
7.3 该部门之物料员需将物料移交下一制程之物料员,物料员之间需核实其数量,数量确定OK后进行物料移交。
7.4 下一制程之物料员将收到之物料再次移交到本生产单位,双方需核对数量,避免有数量上的争议,并签名核实。
7.5 移交签名时需注明移交时间,避免延误时间耽误生产。
八、成品入库作业流程图:
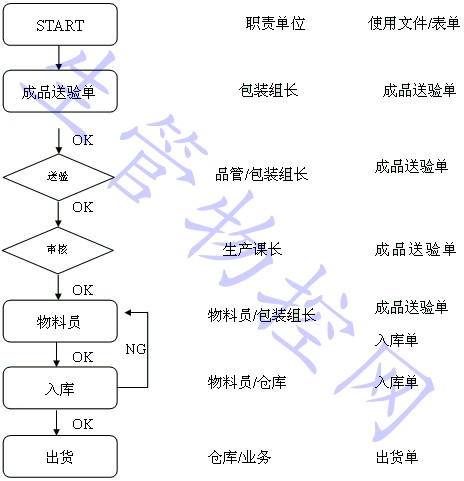
九、作业内容:
9.1 生产包装组长开送验收单交由品管验收,品管验收合格后交于本部门课长审核,并将送验单及成品移交物料员,双方确认其数量后由物料员开具《MT-D-0002入库单》。
9.2 物料员将《MT-D-0002入库单》移交到仓库,并与仓库做物料交接,仓库接到后端业务出货通知后安排出货。
十、生产退料作业流程图:
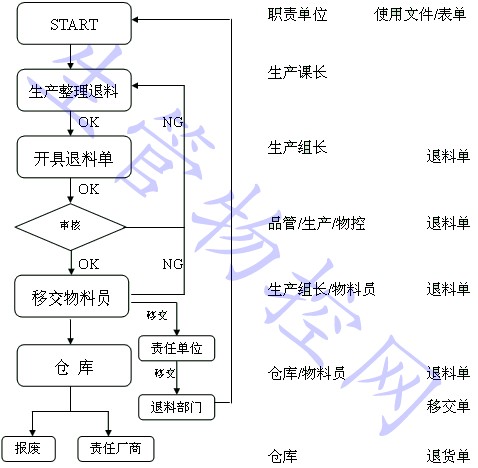
#p#副标题#e#
十一、作业内容:
11.1 生产单位将不良退料整理好后交于单位课长审批,再转品管确认其品质状况,以便退料。
11.2 品管需在退料单上注明其退料处理方式,区分其责任单位。
11.3 品管裁定可以返修的,物料将此物料退到该责任单位处理,责任单位再将返工后的物料移交退料单位。
11.4 退料单经品管认定后,再转交物控审查,让其了解退料状况。
11.5 生产单位将签核完后的退料单再移交物料人员,物料人员确定其数量后在退料单上签名,并将不良品移交仓库。
11.6 移交签名时需注明移交时间,避免延误补料时间。
十二、补料作业流程图:
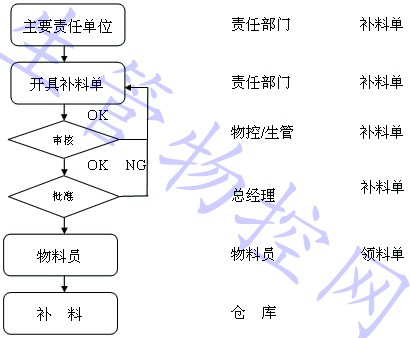
十三、作业内容:
13.1 由主要责任单位填写《MT-D-0006补料单》交由生管/物控人员审查,让其了解补料状况。
13.2 责任部门将生管/物控审查后的《MT-D-0006补料单》呈总经理审批。
13.3 责任部门将总经理审批后的《MT-D-0006补料单》移交物料员并要求补料。
13.4 仓库收到领补料单后发料。
十四、生产预补料:
由于偶尔会产生生产突发状况,导致物料用量不足之情况,此因素较多(eg:工程用量不够、损耗不够、或生产损耗偏高),如果到订单完成时才补料,会导致原物料购买压力大,且交期不容易达到要求,生产可根据自身实际状况预补料,以便生产顺利出货,其流程按补料流程执行!
十五、有关退补料相关规定说明:
15.1退料如有疑问,最终认定单位由工程裁示。
15.2 退料单与补料单一并开出才具有时效性。
15.3 排程的长单每周清一次退料。
15.4 短单每个P/O完成时需清理。
15.5 外发的订单每天都要清理退料,以便即时退补料。
15.6 退料时间生产每天11:00到品管单位,下午16:00-17:00为仓仓库接收退料时间。
十六、相关文件:无
十七、相关附件
17.1《MT-D-0002:入库单》
17.2《MT-D-0003:领料单》
17.3《MT-D-0004:退料单》
17.4《MT-D-0006:补料单》
17.5《MT-D-0012:生产需求单》
17.6《MT-D-0014:在制品移动交接单》