仓库管理控制程序
1.目的
为了使仓库收、发、管作业有序的进行,促使仓库管理规范、标准、高效运作,特制定仓库管理控制程序。
2.适用范围
适用于本公司所有原物料、客供品、半制品的验收、搬运、包装、储存、领发、盘点及仓储安全管理。
3. 职责
仓库管理部门负责及时收、发、存管理及生产退换料、不良品处理等具体事项的落实。
4.定义:
4.1进仓批号:每周进入仓库的物料(包含原材料)或配件所订制的次序编号。
4.2进仓批号的编排法则:
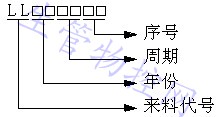
①年份、周期:例2012年,第36周。表示为1136
②序号:为每周内供应商或车间所送货的每种零配件进仓的顺序号。从01开始。
5.作业内容
5.1来料进仓:
5.1.1厂外物料进仓(含外协加工件)
5.1.1.1.仓管收到供应商的送货单后,由仓管员安排卸货,若是紧急物料,仓管人员要优先来料检验人员紧急检验。检验步骤按《来料检验控制程序》操作。
5.1.1.2仓管员根据“采购订单”核对“送货单”,对物料的名称、规格、颜色、数量等信息进行认真核对,如发现“送货单”与“采购订单”有不相符内容,应马上通知采购员(负责此物料的),共同协商解决。
5.1.1.3仓管员核对完毕后,进行收货和签字确认。
5.1.2通知IQC检验
5.1.2.1仓管员收到厂外来料并点数进仓后,开“送检单”,交IQC进行检验,正常情况两个工作日内完成检验,并在“送检单”上注明处理信息,在两个工作日内返还给仓库人员,特急物料4小时内完成检验,同时“送检单”要在2小时内返还给仓库人员。仓库人员按照检验处理结果,对来料进行入库处理。并把物料分区域进行放置。
5.1.3 车间产品进仓
5.1.3.1生产车间把检验合格的配件或成品进仓时,填写“成品合格进仓单”中生产部门填写栏中的相关信息。一并送进仓库交由仓库管理人员,进行进仓处理。
5.1.3.2仓库人员按照进行次序,对车间生产配件或成品,经点进仓数量符合后,在“成品合格进仓单”上仓库进仓员填写栏上填写进仓批号等信息,并办理进仓。并把物料分区域进行放置。
5.2不良品处理
5.2.1不良品退货
5.2.1.1外购物料检验后,经判定“不合格”,IQC在“送检单”处理档上标上数量等相关信息,在物料上贴上不良品标签。
并按《不合格品控制程序》《退料控制程序》处理。
5.2.1.2车间制程不良需退仓的物料,要将数量统计准确,填好“物料(产品)退料进仓单”,由退料车间班组长签名后,交给车间质检员核实,技术质量主管在“物料(产品)退料进仓单”上签名确认,仓库管理员对退料在仓库不良品区域内进行分类放置。并把当月数量呈报供销部和财务部
5.2.2不良品报废
5.2.2.1对外协加工的来料,经核实为不良品物料,仓库管理员把不良数量呈报财务部,并把报废料运送至废料区放置。
5.2.2.2车间生产过程中出现的少量的报废件,经过核实后,由该班组长把物料运送至仓库, 按照《退料控制程序》进行退料处理。仓库管理员把物料分区域进行放置。
5.2.2.3客户退货的退货产品,经过返工返修后的部份报废件,由班组长清点数量后,按照《退料控制程序》进行退料处理。仓库管理员把物料分区域进行放置。
5.2入仓、出仓、补料
5.2.1入仓
5.2.1.1对于入仓的合格来料配件或车间生产件配件。必须贴有检验员检验过的合格标识,无合格标识不予入仓。
5.2.1.2对入生产车间不良品进仓,按照《退料控制程序》进行进仓,进仓数目相符,分类入可进行仓。
5.2.1.2对于客户退货的产品,应放置在临时物料放置区内,并做好进仓记录。待技术人员做完相关分析后,存放在客户退货区内。等待车间进行批量返工返修。
5.2.1.3仓管人员速将物料分类上架,填好标识,同时在“物料卡”作好记录并签名,所有的物料入库、作帐、填卡等工作,并于当天完成。
5.2.2出仓
5.2.2.1仓库管理员按照供销部开出的“产品出厂通知单”。把需要出厂的成品运送至待检区,填写“送检单”交由出厂检验质检员检验。
5.2.2.2对成品出厂后,仓库管理员把成品“出仓单”呈报供销部签字,并做好系统数据录入。
5.2.2.3外协加工配件,出仓、入仓均要求填写“外发加工登记表”。工件出仓外发前必须为检验合格的零配件,并贴有合格标识。无合格标识不予外发。
5.2.2.4车间领料时,仓库管理人员先对“领料单”进行核对,确认无误后均按领料单进行发料出仓。并标明进仓批号,以便于追溯。同时在“物料卡”上做好记录,确保无误并签名。
5.2.3补料
5.2.3.1车间要补料领的物料,车间必须开出“补料单”,单据上要注明补料原因、数量,还必须经过班组长签名,单据符合要求后,仓库才能补发物料。
5.2.3.2特殊情况要补料的,必须经过总经理批示。
5.3帐务处理
5.3.1仓库文员根据“物料(产品)退料进仓单”、“物料产品报废进仓单”、“补料单”和“领料单”做帐,当天的单据要当天完成。
5.3.2仓库员将当天所有的单据分类整理好后,次日9点前分发给财务部。
5.4呆滞料管理
5.4.1仓库部门填写一年内无异动的“呆滞料库存表”,分别呈送总经理。
5.4.2审议核定后如需报废物料由仓库填写“物料╱产品报废申请单”按《不合格品控制程序》处理。
5.4.3如重新使用,仓库管理员把呆滞物料运送至待检区,按《来料检验控制程序》检验进仓处理。#p#副标题#e#
5.5物料的保管与储存
5.5.1仓库物料保管;
a)仓库人员应对仓库内储存区域与料架分布情形非常熟悉。
b)坚持每日巡仓和物料抽查,定期清理仓库呆料、滞料和不合格品。
c)对仓库内保存时间很长的半成品、成品应及时作书面呈报总经理办公室。
d)所有物料必须建立完整的帐目和报表。
e)物料应建立相应的物料卡,确保帐、物、卡一致。
f)贵重物品要入箱上锁,并有专人保管。
5.5.2仓库物料储存;
a)储存应遵循“防水、防火、防压、定点、定位、定量、先进先出”的原则。
b)物料叠放时要做到“上小下大、上轻下重”。
c)易受潮物料,严禁直接摆放于地上,应放货架或卡板进行隔离。
d)呆废料必须分开储存。
e) 物料储存期限:
5.5.3储存区域规划及要求。
5.5.3.1储存区域分为办公区、原料区、成品区、不良品区、报废品区、退料区。
5.5.3.2储存环境要求:通风、通气、通光、干净、防潮,做好日常6S管理。
5.5.3.3仓库常温要控制在5℃-35℃,相对湿度为30%-85%。
5.5.4储存应遵循以下三原则
5.5.4.1先进先出
物料进仓应按次序编写进出先后次序号。每次进仓、出仓均按先后次序进行先进先出原则。
5.5.4.2防火、防潮、防压
A、通道出口畅通,不能堵塞,不能堆放杂物。
B、消防设施配备要齐全。
C、严禁在仓库吸烟,携带火种
D、下班时要关好电源。
E、物料须摆放在卡板或货架上。
F、下雨天要做好防雨工作。
G、下班时要检查门窗、电器设备是否关好,确保物料安全。
H、物料在装卸摆放时,注意上轻下重。
I、物料摆放的高度不要超过2M。
5.5.5定点、定位、定量
A、各类物料要存放事先规定好的区域和位置分类存放,严禁混放。
B、各类物料要定量包装,堆放有序。
5.5.6安全
5.5.6.1专门设立危险品仓库,由专人负责对危险品和易燃易爆品进行管理。
5.5.6.2危险化学物品的管理要遵守“远离火源、水源、电源;严禁混合堆存”的原则。
5.5.6.3仓库内严禁烟火,严禁占用安全通道。
5.5.6.4按消防部门颁布的标准配备消防设备,定期检查。确保其正常使用功能。
5.5.6.5非仓库人员严禁进入仓库存货区(特许人员除外)。
5.5.6.6仓管员要每天巡仓,定期清理仓库物料。
5.6搬运操作。
5.6.1搬运时,上轻下重,注意防护,堆放整齐,匀速行驶。
5.6.2严禁超高、超快、超量搬运物料。
5.6.3搬运时注意轻拿轻放,放置平稳。
5.6.4使用电梯时要遵循《电梯安全使用规定》。
5.7.5下雨时,应对搬运的物料进行防雨措施。
5.7盘点管理。
5.7.1根据公司规定,仓库每月要进行一次月末盘点,年底12月份进行一次年终大盘点。日常工作中仓库要坚持每天自盘。
5.7.2仓库在大盘点前要作好事前准备, 制定盘点方案,并对仓库人员进行培训。
5.7.3初盘完成后,复盘人员进行复盘。对盘点不准确的要重新盘点,直至准确。
5.7.4根据盘点表的盈亏情况,对帐物不符的要查明原因,商讨改善的方案,实施改善。
6.相关文件
6.1《来料检验控制程序》
6.2《不合格品控制程序》
6.3《退料控制程序》
7.相关表格
7.1 呆滞料库存表
7.2 送检单
7.3 领料单
7.4 物料(产品)退料进仓单
7.5 物料产品报废进仓单
7.6 补料单
8. 仓库管理控制程序流程图
为了使仓库收、发、管作业有序的进行,促使仓库管理规范、标准、高效运作,特制定仓库管理控制程序。
2.适用范围
适用于本公司所有原物料、客供品、半制品的验收、搬运、包装、储存、领发、盘点及仓储安全管理。
3. 职责
仓库管理部门负责及时收、发、存管理及生产退换料、不良品处理等具体事项的落实。
4.定义:
4.1进仓批号:每周进入仓库的物料(包含原材料)或配件所订制的次序编号。
4.2进仓批号的编排法则:
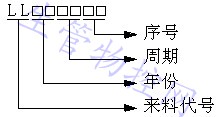
①年份、周期:例2012年,第36周。表示为1136
②序号:为每周内供应商或车间所送货的每种零配件进仓的顺序号。从01开始。
5.作业内容
5.1来料进仓:
5.1.1厂外物料进仓(含外协加工件)
5.1.1.1.仓管收到供应商的送货单后,由仓管员安排卸货,若是紧急物料,仓管人员要优先来料检验人员紧急检验。检验步骤按《来料检验控制程序》操作。
5.1.1.2仓管员根据“采购订单”核对“送货单”,对物料的名称、规格、颜色、数量等信息进行认真核对,如发现“送货单”与“采购订单”有不相符内容,应马上通知采购员(负责此物料的),共同协商解决。
5.1.1.3仓管员核对完毕后,进行收货和签字确认。
5.1.2通知IQC检验
5.1.2.1仓管员收到厂外来料并点数进仓后,开“送检单”,交IQC进行检验,正常情况两个工作日内完成检验,并在“送检单”上注明处理信息,在两个工作日内返还给仓库人员,特急物料4小时内完成检验,同时“送检单”要在2小时内返还给仓库人员。仓库人员按照检验处理结果,对来料进行入库处理。并把物料分区域进行放置。
5.1.3 车间产品进仓
5.1.3.1生产车间把检验合格的配件或成品进仓时,填写“成品合格进仓单”中生产部门填写栏中的相关信息。一并送进仓库交由仓库管理人员,进行进仓处理。
5.1.3.2仓库人员按照进行次序,对车间生产配件或成品,经点进仓数量符合后,在“成品合格进仓单”上仓库进仓员填写栏上填写进仓批号等信息,并办理进仓。并把物料分区域进行放置。
5.2不良品处理
5.2.1不良品退货
5.2.1.1外购物料检验后,经判定“不合格”,IQC在“送检单”处理档上标上数量等相关信息,在物料上贴上不良品标签。
并按《不合格品控制程序》《退料控制程序》处理。
5.2.1.2车间制程不良需退仓的物料,要将数量统计准确,填好“物料(产品)退料进仓单”,由退料车间班组长签名后,交给车间质检员核实,技术质量主管在“物料(产品)退料进仓单”上签名确认,仓库管理员对退料在仓库不良品区域内进行分类放置。并把当月数量呈报供销部和财务部
5.2.2不良品报废
5.2.2.1对外协加工的来料,经核实为不良品物料,仓库管理员把不良数量呈报财务部,并把报废料运送至废料区放置。
5.2.2.2车间生产过程中出现的少量的报废件,经过核实后,由该班组长把物料运送至仓库, 按照《退料控制程序》进行退料处理。仓库管理员把物料分区域进行放置。
5.2.2.3客户退货的退货产品,经过返工返修后的部份报废件,由班组长清点数量后,按照《退料控制程序》进行退料处理。仓库管理员把物料分区域进行放置。
5.2入仓、出仓、补料
5.2.1入仓
5.2.1.1对于入仓的合格来料配件或车间生产件配件。必须贴有检验员检验过的合格标识,无合格标识不予入仓。
5.2.1.2对入生产车间不良品进仓,按照《退料控制程序》进行进仓,进仓数目相符,分类入可进行仓。
5.2.1.2对于客户退货的产品,应放置在临时物料放置区内,并做好进仓记录。待技术人员做完相关分析后,存放在客户退货区内。等待车间进行批量返工返修。
5.2.1.3仓管人员速将物料分类上架,填好标识,同时在“物料卡”作好记录并签名,所有的物料入库、作帐、填卡等工作,并于当天完成。
5.2.2出仓
5.2.2.1仓库管理员按照供销部开出的“产品出厂通知单”。把需要出厂的成品运送至待检区,填写“送检单”交由出厂检验质检员检验。
5.2.2.2对成品出厂后,仓库管理员把成品“出仓单”呈报供销部签字,并做好系统数据录入。
5.2.2.3外协加工配件,出仓、入仓均要求填写“外发加工登记表”。工件出仓外发前必须为检验合格的零配件,并贴有合格标识。无合格标识不予外发。
5.2.2.4车间领料时,仓库管理人员先对“领料单”进行核对,确认无误后均按领料单进行发料出仓。并标明进仓批号,以便于追溯。同时在“物料卡”上做好记录,确保无误并签名。
5.2.3补料
5.2.3.1车间要补料领的物料,车间必须开出“补料单”,单据上要注明补料原因、数量,还必须经过班组长签名,单据符合要求后,仓库才能补发物料。
5.2.3.2特殊情况要补料的,必须经过总经理批示。
5.3帐务处理
5.3.1仓库文员根据“物料(产品)退料进仓单”、“物料产品报废进仓单”、“补料单”和“领料单”做帐,当天的单据要当天完成。
5.3.2仓库员将当天所有的单据分类整理好后,次日9点前分发给财务部。
5.4呆滞料管理
5.4.1仓库部门填写一年内无异动的“呆滞料库存表”,分别呈送总经理。
5.4.2审议核定后如需报废物料由仓库填写“物料╱产品报废申请单”按《不合格品控制程序》处理。
5.4.3如重新使用,仓库管理员把呆滞物料运送至待检区,按《来料检验控制程序》检验进仓处理。#p#副标题#e#
5.5物料的保管与储存
5.5.1仓库物料保管;
a)仓库人员应对仓库内储存区域与料架分布情形非常熟悉。
b)坚持每日巡仓和物料抽查,定期清理仓库呆料、滞料和不合格品。
c)对仓库内保存时间很长的半成品、成品应及时作书面呈报总经理办公室。
d)所有物料必须建立完整的帐目和报表。
e)物料应建立相应的物料卡,确保帐、物、卡一致。
f)贵重物品要入箱上锁,并有专人保管。
5.5.2仓库物料储存;
a)储存应遵循“防水、防火、防压、定点、定位、定量、先进先出”的原则。
b)物料叠放时要做到“上小下大、上轻下重”。
c)易受潮物料,严禁直接摆放于地上,应放货架或卡板进行隔离。
d)呆废料必须分开储存。
e) 物料储存期限:
5.5.3储存区域规划及要求。
5.5.3.1储存区域分为办公区、原料区、成品区、不良品区、报废品区、退料区。
5.5.3.2储存环境要求:通风、通气、通光、干净、防潮,做好日常6S管理。
5.5.3.3仓库常温要控制在5℃-35℃,相对湿度为30%-85%。
5.5.4储存应遵循以下三原则
5.5.4.1先进先出
物料进仓应按次序编写进出先后次序号。每次进仓、出仓均按先后次序进行先进先出原则。
5.5.4.2防火、防潮、防压
A、通道出口畅通,不能堵塞,不能堆放杂物。
B、消防设施配备要齐全。
C、严禁在仓库吸烟,携带火种
D、下班时要关好电源。
E、物料须摆放在卡板或货架上。
F、下雨天要做好防雨工作。
G、下班时要检查门窗、电器设备是否关好,确保物料安全。
H、物料在装卸摆放时,注意上轻下重。
I、物料摆放的高度不要超过2M。
5.5.5定点、定位、定量
A、各类物料要存放事先规定好的区域和位置分类存放,严禁混放。
B、各类物料要定量包装,堆放有序。
5.5.6安全
5.5.6.1专门设立危险品仓库,由专人负责对危险品和易燃易爆品进行管理。
5.5.6.2危险化学物品的管理要遵守“远离火源、水源、电源;严禁混合堆存”的原则。
5.5.6.3仓库内严禁烟火,严禁占用安全通道。
5.5.6.4按消防部门颁布的标准配备消防设备,定期检查。确保其正常使用功能。
5.5.6.5非仓库人员严禁进入仓库存货区(特许人员除外)。
5.5.6.6仓管员要每天巡仓,定期清理仓库物料。
5.6搬运操作。
5.6.1搬运时,上轻下重,注意防护,堆放整齐,匀速行驶。
5.6.2严禁超高、超快、超量搬运物料。
5.6.3搬运时注意轻拿轻放,放置平稳。
5.6.4使用电梯时要遵循《电梯安全使用规定》。
5.7.5下雨时,应对搬运的物料进行防雨措施。
5.7盘点管理。
5.7.1根据公司规定,仓库每月要进行一次月末盘点,年底12月份进行一次年终大盘点。日常工作中仓库要坚持每天自盘。
5.7.2仓库在大盘点前要作好事前准备, 制定盘点方案,并对仓库人员进行培训。
5.7.3初盘完成后,复盘人员进行复盘。对盘点不准确的要重新盘点,直至准确。
5.7.4根据盘点表的盈亏情况,对帐物不符的要查明原因,商讨改善的方案,实施改善。
6.相关文件
6.1《来料检验控制程序》
6.2《不合格品控制程序》
6.3《退料控制程序》
7.相关表格
7.1 呆滞料库存表
7.2 送检单
7.3 领料单
7.4 物料(产品)退料进仓单
7.5 物料产品报废进仓单
7.6 补料单
8. 仓库管理控制程序流程图
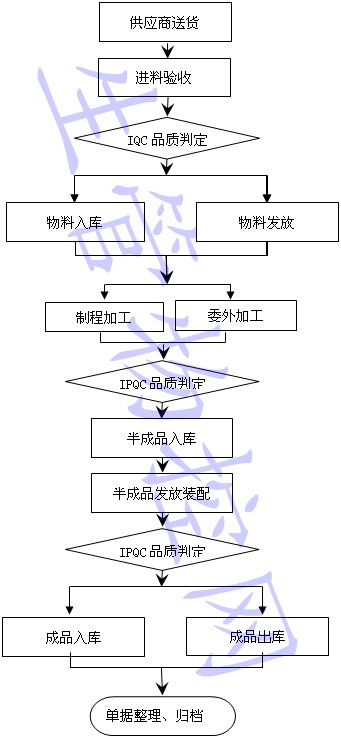