适用于缺陷管理的六西格玛法
σ(中文读音“西格玛”)在统计学上是指“标准差”,六西格玛(6σ)就是“6倍标准差”,在质量上表示每100万个产品的不良品率(PPM)低于3.4。6σ管理的要求是在整个流程中每100万个产品的缺陷率低于3.4,这对企业来说是一个很严格的要求。下图是3~6个西格玛水平的缺陷数比较。
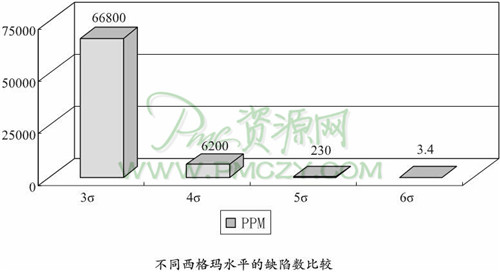
目前绝大多数业内领先企业的运作水平都在3σ~4σ之间,也就是在每100万个产品中有6200~66800个不良品,每年所产生的缺陷成本需要用15%~30%的销售额来弥补。根据麦肯锡公司的调查和研究,如果一个3σ企业组织通过对所有资源的改进,把西格玛水平由3提高到4,获得的收益将非常可观:利润率增加20%;产能提高12%~18%;雇员减少12%;资本投入降低10%~30%(见下表所示)。当企业达到6σ管理水平后,用于弥补缺陷的销售额则可以下降到5%。从这些数据中,我们不难看到水平的威力。
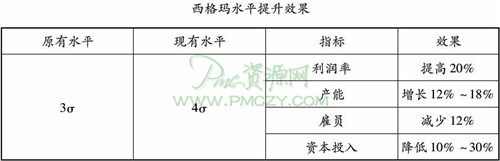
一、实施6σ管理的前提
6σ管理有两层含义:一是评价缺陷的标准,二是实现目标的动力。实施6σ管理的前提,是要进行理念更新。
1.评价缺陷的标准。要以6σ为标准评价缺陷,改变“我一直都这么做,而且做得很好”的惯性思维,企业上下都要树立一个新的理念,评价的标准就是6σ。也许企业原来管理方式的效果也不错,但与6σ的目标相比,肯定还有很大的差距。
2.实现目标的动力。要以6σ为目标来推动改进,通过实施6σ管理,看清自身的水平和差距,不断改进,努力提升水平、缩小距离,最终实现目标。
二、实施6σ管理的七个步骤
按照摩托罗拉公司的成功经验,6σ管理的实施需要经过以下七个步骤。
1.寻找明确问题(Select a problem and describe it clearly)。找出和说明需要改正的问题,并着手解决。
2.研究现行系统(Study the present system)。收集现行生产方法的数据,进行整理和研究。
3.鉴别问题成因(Identify possible causes)。采取不同方法,如头脑风暴法、控制图法、鱼骨图法等,分析鉴定问题产生的原因。
4.制定贯彻方案(Plan and implement a solution)。集中各方力量,制定解决方案,并贯彻执行。
5.评价执行效果(Evaluate effects)。通过相关数据的收集和分析,对解决方法是否有效进行评估。
6.规范有效方法(Standardize any effective solutions)。将经证明有成效的方法制度化,制定为工作规范并落实执行。
7.总结开创未来(Reflect on process and develop future plans)。在对实施过程进行总结的基础上,制订未来发展计划。
#p#副标题#e#
三、6σ管理的组织结构
6σ管理的组织结构分为6个层次。如下图所示。
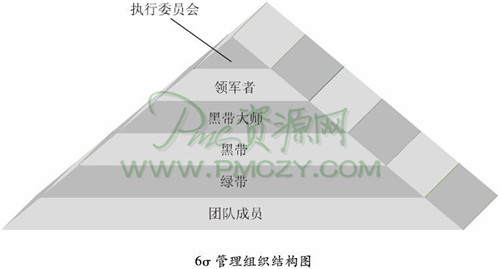
1.执行委员会。执行委员会是企业实施6σ管理的最高领导机构,主要成员是企业高层领导,职责是设立初始阶段的各种职位、确定具体的改进项目及改进次序、分配资源、协调各方面问题、对项目进展进行评估等。
2.领军者。领军者由副总裁以上的高层领导担任,具体职责是为项目设定目标、方向和范围,协调项目所需资源,处理项目小组之间的问题。
3.黑带大师。6σ管理专家的最高级别,通常是统计专家,负责提供技术指导。主要工作是培训黑带,同时实现执行负责人提出的工作目标。黑带大师的人数很少,只有黑带的1/10左右。
4.黑带。6σ管理的中坚力量,由企业内部选拔,全职实施6σ管理,在经培训取得黑带认证后,担任项目小组负责人,领导项目实施,完成改善目标,同时负责培训绿带。
5.绿带。6σ管理中的兼职人员,经过培训后负责一些难度较小的项目小组,或作为其他项目小组的成员,是众多底线收益项目的执行者。
6.团队成员。6σ管理的基础,参加所有会议和相关培训,按照流程开展工作,完成项目任务。
通常每1000名员工中,应配备黑带大师1名,黑带10名,绿带50~70名。
案例
某汽车内胎公司为了实施6σ管理,专门聘请了一位黑带大师,负责公司的黑带培训。公司从各地工厂共选出9名员工参加培训,培训分为理论和实践两部分,时间为1年。前半年每个月集中1周时间上课,其他时间到工厂实践,了解不同产品的生产过程和管理氛围。后半年参加培训的人员回到工厂,各自负责具体项目,并确保自己负责的项目能够真正实现流程改善、成本削减。随后他们才有可能成为黑带。
由于重视对骨干的培训,该公司的6σ管理有了很大成效。比如轮胎是由多层材料组成的,在成型时各层面需要紧密结合才能保证质量。为了解决夏天湿度大、温度高的环境问题,项目组通过改进制造工艺和更新冷却设备,使产品黏合度得到显著提高。各地分公司也是捷报频传,山东分公司在不增加生产设备和人员的情况下,生产效率提升了40%,废品率比同期降低了一半。昆山分公司在骨干的带动下,投产半年内日产量提高到1万条。
点评
从案例中我们可以看到黑带大师和黑带在6σ管理中的作用。黑带大师的作用是培养黑带,提升他们的能力。而黑带的作用,则在于具体项目的实施,确保项目能取得成效。
#p#副标题#e#
四、实施6σ管理的五个环节
实现6σ管理水平,是一个循序渐进的过程,需要有一套完善的管理流程。不少公司都提出了自己的流程,其中通用电气公司总结的DMAIC模式,被普遍认为更具操作性。
所谓的DMAIC,包括了五个环节:界定(Define)、测量(Measure)、分析(Analyze)、改进(Improve)、控制(Control)。如下图所示。
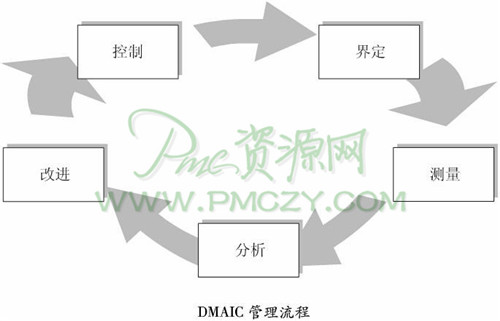
1.界定。分析问题产生的原因,找出其中影响最大的原因,明确关注重点和需要解决的问题。首先要准确定位,其次要把需要解决的问题具体化。比如某企业的产出率只有70%左右,主要工序中有一道工序产出率比其他工序约低20%,经分析主要是由于微量元素超标造成大量不合格品所致,于是可以把问题界定为“微量元素超标引起的不合格品率上升”。
2.测量。对已经界定的原因进行测量,根据数据和事实确定目标与方向。如对于已经界定的微量元素超标问题,许多人认为需要更新工艺和设备,但经过数据分析,发现微量元素超标并不是工艺和设备所致,而是因为存在某些其他的因素。如果能及时找出这些因素并加以控制,就可以降低为解决该问题所付出的代价。
3.分析。通过对数据和现象的分析,从表象入手,层层深入,最后确定影响质量的关键因素。如某企业的产出率水平不稳定,高的时候可以达到95%,低的时候只有75%左右。初步分析的结果显示,可能的因素是操作和材料。但进一步的数据分析排除了材料因素的可能性,因为轮班之间的产出率差距也是很大的。在随后对轮班做的分析中发现,主要问题在于反应槽加温时间的控制方面,而更深入的分析表明,当加温时间控制在50分钟以上时,产出率可以超过92%。而针对分析进行改进的结果表明,项目组对原因的分析准确到位。
4.改进。运用项目管理工具,针对关键因素,通过试验比较法,选定最佳改进方案。如某企业为缩短生产周期,需要将一道工序的生产时间压缩到3分钟以内。经分析,影响生产时间的因素有三个,分别是作业单元、操作方法和生产工具。相关试验表明,生产工具改进对生产时间影响不大,所以改变集中在作业单位和操作方法两个方面,改变的结果是该工序的生产时间由原来的3.7分钟压缩到2.6分钟左右。
5.控制。通过制订控制计划,采取防控措施,实现对缺陷的有效控制。如某企业针对加工过程中的加压时间不足和工装安装错误两个问题,进行了在线监测和防错装置,从源头上抑制缺陷出现的可能,有效地保证了改进效果的持续性。
#p#副标题#e#
五、6σ管理中需注意的三个问题
6σ管理在我国企业的应用,既有成功的经验,也有失败的教训。虽然失败的原因各不相同,但最主要的是三个问题。首先是对6σ管理的认识有偏差,其次是实施6σ管理的方法不对头,最后是实施6σ管理的时机欠成熟。
1.认识有偏差。一是不够重视,高层领导的参与度较低。二是注重形式,工作集中在套路方面。三是偏重技术,忽视统计方法与实际问题的匹配度。
2.方法不对头。一是机械模仿,不顾实际照抄照搬。二是缺乏统筹,对项目的推进没有规划。三是不能持续,新鲜劲过后又恢复到老样子。
3.时机欠成熟。一是基础太差,没有具备相应的条件,如管理混乱、数据缺乏。二是操之过急,没有经过相应的培训,着急上马,结果是处处卡壳。
失败的教训告诉我们,任何方法都有一定的局限性,对实施的环境有各不相同的要求。如何做到企业生产的特点和运作方法的特点相融合,关键是要切合实际,方法再好,如果企业不具备实施的条件也是白搭,到头来也只能是浪费时间、人力和物力。在应用先进运作方法之前,生产总监必须对方法进行深入的了解和研究,并对其是否符合企业的实际情况进行考量,不能人云亦云。只要是企业还不具备实施的条件,就要暂缓该方法的应用,等到企业条件经过改进达到相应的要求时,再开始应用。另外,在应用先进方法时,不能机械套用,一成不变。在实际应用中,企业必须根据各自的生产环境进行适当的调整,以使方法更适合企业的特点。比如企业目前并不具备全面推行6σ管理的实力,那么可以从某个项目或某个环节开始做起,逐步开展、逐步推广。
案例
太钢高层领导经过与全球钢铁企业的交流活动,了解到国外钢铁企业的6σ管理。为实现建设全球最具竞争力的不锈钢企业战略目标,太钢于是决定导入6σ管理。
太钢导入6σ管理采取的是自上而下的推进方式,集团董事长和总经理作为总倡导者,总工程师亲自挂帅,成立专职部门,制定了愿景和规划,健全了制度体系。其主要步骤与过程是:管理者参与培训、统一认知,对管理和技术骨干进行基础知识培训,试点单位实施6σ黑带改进项目,全面铺开培训,全面开展6σ改进项目。
太钢选择了不锈钢冷轧板和冷轧硅钢两个重点产品作为切入点,以质量、交货期、产能为突破口,根据改进问题的需要选择能牵头解决问题的管理人员和技术骨干作为黑带或绿带学员,边学习边解决问题。在确立首批16个黑带改进项目的同时,举办了黑带培训班和绿带培训班。随后又进一步扩大培训对象和人数,按照培训对象的不同,确定不同的培训内容和培训方法,并分阶段逐步实施培训。
根据公司战略目标、年度预算等,经过项目预选和阶段学习、评审后,分批确定了改进项目,涉及了20多个单位、部门,逐渐覆盖了生产经营全流程,项目的类型更加多样化,包括质量改进、缩短交货期,计量检测、设备保障、能源管理等。
太钢在实施6σ管理的初期也遇到了不少障碍与挑战。比如管理类项目的数据积累不足,项目进展缓慢等。但随着太钢信息化系统的上线运行、6σ管理的强化和项目覆盖面的拓展,上述的问题都逐步得到了改进。
太钢通过实施6σ管理,实现了人才和效益双丰收。经过系统培训,已有300余人通过了国家相关考试。在黑带、绿带的带领下,太钢改进项目收益颇丰,2005年15个黑带项目改进后年度获益近9000万元,2006年项目年收益超过2亿元。
点评
太钢在推进6σ管理方面能取得成功,主要有五个方面的原因:第一是领导重视,高层领导亲自参与,定位清晰、目标明确;第二是准备充分,培训从各级领导开始,逐步扩展到项目骨干;第三是导入得法,从重点产品入手,逐步扩大规模和范围;第四是骨干推动,通过重点培训和组织参考的形式,提升骨干能力、推动项目进程;第五是管理先行,通过建立专职部门,配套各种制度,为项目的顺利实施奠定了基础。
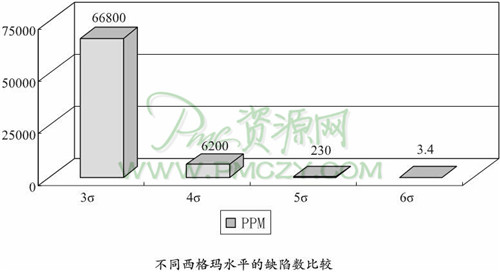
目前绝大多数业内领先企业的运作水平都在3σ~4σ之间,也就是在每100万个产品中有6200~66800个不良品,每年所产生的缺陷成本需要用15%~30%的销售额来弥补。根据麦肯锡公司的调查和研究,如果一个3σ企业组织通过对所有资源的改进,把西格玛水平由3提高到4,获得的收益将非常可观:利润率增加20%;产能提高12%~18%;雇员减少12%;资本投入降低10%~30%(见下表所示)。当企业达到6σ管理水平后,用于弥补缺陷的销售额则可以下降到5%。从这些数据中,我们不难看到水平的威力。
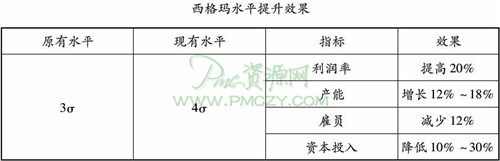
一、实施6σ管理的前提
6σ管理有两层含义:一是评价缺陷的标准,二是实现目标的动力。实施6σ管理的前提,是要进行理念更新。
1.评价缺陷的标准。要以6σ为标准评价缺陷,改变“我一直都这么做,而且做得很好”的惯性思维,企业上下都要树立一个新的理念,评价的标准就是6σ。也许企业原来管理方式的效果也不错,但与6σ的目标相比,肯定还有很大的差距。
2.实现目标的动力。要以6σ为目标来推动改进,通过实施6σ管理,看清自身的水平和差距,不断改进,努力提升水平、缩小距离,最终实现目标。
二、实施6σ管理的七个步骤
按照摩托罗拉公司的成功经验,6σ管理的实施需要经过以下七个步骤。
1.寻找明确问题(Select a problem and describe it clearly)。找出和说明需要改正的问题,并着手解决。
2.研究现行系统(Study the present system)。收集现行生产方法的数据,进行整理和研究。
3.鉴别问题成因(Identify possible causes)。采取不同方法,如头脑风暴法、控制图法、鱼骨图法等,分析鉴定问题产生的原因。
4.制定贯彻方案(Plan and implement a solution)。集中各方力量,制定解决方案,并贯彻执行。
5.评价执行效果(Evaluate effects)。通过相关数据的收集和分析,对解决方法是否有效进行评估。
6.规范有效方法(Standardize any effective solutions)。将经证明有成效的方法制度化,制定为工作规范并落实执行。
7.总结开创未来(Reflect on process and develop future plans)。在对实施过程进行总结的基础上,制订未来发展计划。
#p#副标题#e#
三、6σ管理的组织结构
6σ管理的组织结构分为6个层次。如下图所示。
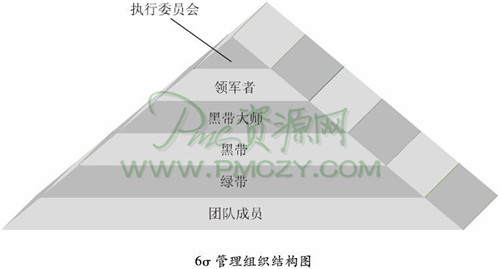
1.执行委员会。执行委员会是企业实施6σ管理的最高领导机构,主要成员是企业高层领导,职责是设立初始阶段的各种职位、确定具体的改进项目及改进次序、分配资源、协调各方面问题、对项目进展进行评估等。
2.领军者。领军者由副总裁以上的高层领导担任,具体职责是为项目设定目标、方向和范围,协调项目所需资源,处理项目小组之间的问题。
3.黑带大师。6σ管理专家的最高级别,通常是统计专家,负责提供技术指导。主要工作是培训黑带,同时实现执行负责人提出的工作目标。黑带大师的人数很少,只有黑带的1/10左右。
4.黑带。6σ管理的中坚力量,由企业内部选拔,全职实施6σ管理,在经培训取得黑带认证后,担任项目小组负责人,领导项目实施,完成改善目标,同时负责培训绿带。
5.绿带。6σ管理中的兼职人员,经过培训后负责一些难度较小的项目小组,或作为其他项目小组的成员,是众多底线收益项目的执行者。
6.团队成员。6σ管理的基础,参加所有会议和相关培训,按照流程开展工作,完成项目任务。
通常每1000名员工中,应配备黑带大师1名,黑带10名,绿带50~70名。
案例
某汽车内胎公司为了实施6σ管理,专门聘请了一位黑带大师,负责公司的黑带培训。公司从各地工厂共选出9名员工参加培训,培训分为理论和实践两部分,时间为1年。前半年每个月集中1周时间上课,其他时间到工厂实践,了解不同产品的生产过程和管理氛围。后半年参加培训的人员回到工厂,各自负责具体项目,并确保自己负责的项目能够真正实现流程改善、成本削减。随后他们才有可能成为黑带。
由于重视对骨干的培训,该公司的6σ管理有了很大成效。比如轮胎是由多层材料组成的,在成型时各层面需要紧密结合才能保证质量。为了解决夏天湿度大、温度高的环境问题,项目组通过改进制造工艺和更新冷却设备,使产品黏合度得到显著提高。各地分公司也是捷报频传,山东分公司在不增加生产设备和人员的情况下,生产效率提升了40%,废品率比同期降低了一半。昆山分公司在骨干的带动下,投产半年内日产量提高到1万条。
点评
从案例中我们可以看到黑带大师和黑带在6σ管理中的作用。黑带大师的作用是培养黑带,提升他们的能力。而黑带的作用,则在于具体项目的实施,确保项目能取得成效。
#p#副标题#e#
四、实施6σ管理的五个环节
实现6σ管理水平,是一个循序渐进的过程,需要有一套完善的管理流程。不少公司都提出了自己的流程,其中通用电气公司总结的DMAIC模式,被普遍认为更具操作性。
所谓的DMAIC,包括了五个环节:界定(Define)、测量(Measure)、分析(Analyze)、改进(Improve)、控制(Control)。如下图所示。
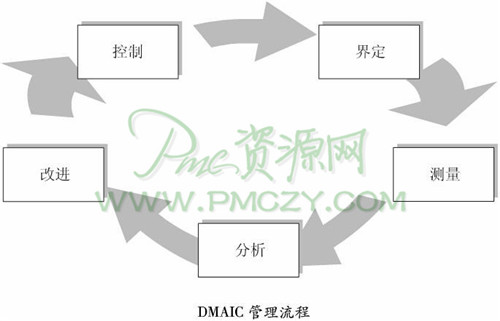
1.界定。分析问题产生的原因,找出其中影响最大的原因,明确关注重点和需要解决的问题。首先要准确定位,其次要把需要解决的问题具体化。比如某企业的产出率只有70%左右,主要工序中有一道工序产出率比其他工序约低20%,经分析主要是由于微量元素超标造成大量不合格品所致,于是可以把问题界定为“微量元素超标引起的不合格品率上升”。
2.测量。对已经界定的原因进行测量,根据数据和事实确定目标与方向。如对于已经界定的微量元素超标问题,许多人认为需要更新工艺和设备,但经过数据分析,发现微量元素超标并不是工艺和设备所致,而是因为存在某些其他的因素。如果能及时找出这些因素并加以控制,就可以降低为解决该问题所付出的代价。
3.分析。通过对数据和现象的分析,从表象入手,层层深入,最后确定影响质量的关键因素。如某企业的产出率水平不稳定,高的时候可以达到95%,低的时候只有75%左右。初步分析的结果显示,可能的因素是操作和材料。但进一步的数据分析排除了材料因素的可能性,因为轮班之间的产出率差距也是很大的。在随后对轮班做的分析中发现,主要问题在于反应槽加温时间的控制方面,而更深入的分析表明,当加温时间控制在50分钟以上时,产出率可以超过92%。而针对分析进行改进的结果表明,项目组对原因的分析准确到位。
4.改进。运用项目管理工具,针对关键因素,通过试验比较法,选定最佳改进方案。如某企业为缩短生产周期,需要将一道工序的生产时间压缩到3分钟以内。经分析,影响生产时间的因素有三个,分别是作业单元、操作方法和生产工具。相关试验表明,生产工具改进对生产时间影响不大,所以改变集中在作业单位和操作方法两个方面,改变的结果是该工序的生产时间由原来的3.7分钟压缩到2.6分钟左右。
5.控制。通过制订控制计划,采取防控措施,实现对缺陷的有效控制。如某企业针对加工过程中的加压时间不足和工装安装错误两个问题,进行了在线监测和防错装置,从源头上抑制缺陷出现的可能,有效地保证了改进效果的持续性。
#p#副标题#e#
五、6σ管理中需注意的三个问题
6σ管理在我国企业的应用,既有成功的经验,也有失败的教训。虽然失败的原因各不相同,但最主要的是三个问题。首先是对6σ管理的认识有偏差,其次是实施6σ管理的方法不对头,最后是实施6σ管理的时机欠成熟。
1.认识有偏差。一是不够重视,高层领导的参与度较低。二是注重形式,工作集中在套路方面。三是偏重技术,忽视统计方法与实际问题的匹配度。
2.方法不对头。一是机械模仿,不顾实际照抄照搬。二是缺乏统筹,对项目的推进没有规划。三是不能持续,新鲜劲过后又恢复到老样子。
3.时机欠成熟。一是基础太差,没有具备相应的条件,如管理混乱、数据缺乏。二是操之过急,没有经过相应的培训,着急上马,结果是处处卡壳。
失败的教训告诉我们,任何方法都有一定的局限性,对实施的环境有各不相同的要求。如何做到企业生产的特点和运作方法的特点相融合,关键是要切合实际,方法再好,如果企业不具备实施的条件也是白搭,到头来也只能是浪费时间、人力和物力。在应用先进运作方法之前,生产总监必须对方法进行深入的了解和研究,并对其是否符合企业的实际情况进行考量,不能人云亦云。只要是企业还不具备实施的条件,就要暂缓该方法的应用,等到企业条件经过改进达到相应的要求时,再开始应用。另外,在应用先进方法时,不能机械套用,一成不变。在实际应用中,企业必须根据各自的生产环境进行适当的调整,以使方法更适合企业的特点。比如企业目前并不具备全面推行6σ管理的实力,那么可以从某个项目或某个环节开始做起,逐步开展、逐步推广。
案例
太钢高层领导经过与全球钢铁企业的交流活动,了解到国外钢铁企业的6σ管理。为实现建设全球最具竞争力的不锈钢企业战略目标,太钢于是决定导入6σ管理。
太钢导入6σ管理采取的是自上而下的推进方式,集团董事长和总经理作为总倡导者,总工程师亲自挂帅,成立专职部门,制定了愿景和规划,健全了制度体系。其主要步骤与过程是:管理者参与培训、统一认知,对管理和技术骨干进行基础知识培训,试点单位实施6σ黑带改进项目,全面铺开培训,全面开展6σ改进项目。
太钢选择了不锈钢冷轧板和冷轧硅钢两个重点产品作为切入点,以质量、交货期、产能为突破口,根据改进问题的需要选择能牵头解决问题的管理人员和技术骨干作为黑带或绿带学员,边学习边解决问题。在确立首批16个黑带改进项目的同时,举办了黑带培训班和绿带培训班。随后又进一步扩大培训对象和人数,按照培训对象的不同,确定不同的培训内容和培训方法,并分阶段逐步实施培训。
根据公司战略目标、年度预算等,经过项目预选和阶段学习、评审后,分批确定了改进项目,涉及了20多个单位、部门,逐渐覆盖了生产经营全流程,项目的类型更加多样化,包括质量改进、缩短交货期,计量检测、设备保障、能源管理等。
太钢在实施6σ管理的初期也遇到了不少障碍与挑战。比如管理类项目的数据积累不足,项目进展缓慢等。但随着太钢信息化系统的上线运行、6σ管理的强化和项目覆盖面的拓展,上述的问题都逐步得到了改进。
太钢通过实施6σ管理,实现了人才和效益双丰收。经过系统培训,已有300余人通过了国家相关考试。在黑带、绿带的带领下,太钢改进项目收益颇丰,2005年15个黑带项目改进后年度获益近9000万元,2006年项目年收益超过2亿元。
点评
太钢在推进6σ管理方面能取得成功,主要有五个方面的原因:第一是领导重视,高层领导亲自参与,定位清晰、目标明确;第二是准备充分,培训从各级领导开始,逐步扩展到项目骨干;第三是导入得法,从重点产品入手,逐步扩大规模和范围;第四是骨干推动,通过重点培训和组织参考的形式,提升骨干能力、推动项目进程;第五是管理先行,通过建立专职部门,配套各种制度,为项目的顺利实施奠定了基础。