不合格品控制制度
1. 目的
对不合格品(含原辅料)进行严格控制,防止不良品流出,确保出厂产品质量符合顾客要求。
2. 范围
适用于进货检验,生产全过程及出厂后发生的不合格品的控制。
3. 定义
为满足要求
4. 职责
4.1 各责任部门负责不合格品的隔离。
4.2 质检员负责不合格品的鉴别、标识。
4.3 质量部组织不合格品的评审。
4.4 生产部、销售部、市场研发部、设备部、生产工段参与不合格品的评审。
4.5 不合格品的发生部门按不合格品评审结果处置不合格品。
5. 不合格品控制程序流程图
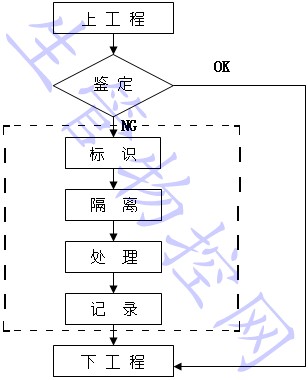
6. 内容及要求:
6.1 不合格品的分类
6.1.1 原辅材料的不合格品
6.1.2 工序产品的不合格品
6.1.2.1 正常消耗原因(试机、停机等原因)造成的不合格品
6.1.2.2 非正常消耗原因造成的不合格品
6.1.3 成品的不合格品
6.2 不合格品的确认
6.2.1 不能满足公司质量标准或顾客要求的产品均为不合格品。
6.2.2 操作人员负责自检过程不合格品的确认。
6.2.3 质检员负责检验和测试过程不合格品的确认。
6.2.4 业务员负责交付后不合格品的确认。#p#副标题#e#
6.3 不合格品的隔离
6.3.1 工序检验过程中出现的不合格品,由工段长和班长负责采取隔离措施。
6.3.2 最终检验不合格品应由质检员同跟班班长采取隔离措施,仓库、工段应提供不合格品放置区,以便不合格品能有效隔离。
6.3.3 原材料不合格品、出厂前检出的不合格品、顾客退回的不合格品、生产工段退回仓库的不合格品由库房采取隔离措施。
6.3.4 对于工序产品和成品出现的大批量的不合格品,质检员依照《检验和测试状态识别程序》对其标识及时上报质管部部长,以便及时处置。
6.4 原辅材料不合格品的评审、处置。
6.4.1 不合格品的评审、处置、标识。
6.4.1.1 原辅材料不合格品发生后12小时内,质管部、供应部必须对其进行评审,最晚不能超过24小时。
6.4.1.2 评审的原则:能否降等使用。
6.4.1.3 原辅材料不合格品的处置方式。
①降等接收;
②退货。
A.检验后拒收的原辅材料,由质管部部长确认后交供应部依据用料需求状况,以决议结果处理。
B.呆滞料判定未丧失主功能者,以退回分供方、折价出售或变更为其他用料,否则以报废处置。
6.4.1.4 质管部将处置结果记录在“原辅材料检验报告”的不合格品处置一栏中。
6.4.1.5 库管员依据“原辅材料检验报告”对处置后的不合格品进行标识。
6.4.1.6 原辅材料不合格品处置后的标识
A.降等接收的不合格品按区域分类码放,标明实际等级。
B.退货:隔离堆放,用“拒收标签”标识。
6.4.1.7 供应部负责与分供方联络退货的有关事宜,填写“退货记录”。
6.4.2 工序产品、成品的不合格品的评审、处置。
6.4.2.1 非正常消耗原因造成的不合格品,由工段主任、质检员、跟班班长现场处置,并在“过程检验记录”上记录。
6.4.2.2 非正常消耗原因造成的不合格品和成品的不合格品的评审。
①对偶然发生的且价值较小的单件或小批量的不合格品,直接由质检员处理,不再进行不合格的评审,但对处置结果必须在“过程检验记录”上记录。
②对价值较大的不合格品由责任部门以书面形式上报质管部,由质管部组织供应部、销售部、生产技术部、设备管理部、工段对不合格品进行评审;填写“不合格品评审处置报告”一式两份,质管部、生产技术部各一份;评审时间不能超过不合格品发生后24小时。#p#副标题#e#
6.4.2.3 评审内容
①不合格品产生的原因:
供应部从原辅材料的角度分析;生产技术部从技术的角度分析;设备管理部从设备的精度、完好程度分析;工段从操作的角度分析。
②不合格品的处置方式
6.4.2.4 不合格品处置方式的分类
①返工;
②返修;
③让步接收;
④报废:
⑤降等处理。
6.4.2.5 不合格品处置方式的标识
①返工、返修产品用紫牌标识;
②让步接收产品用蓝牌标识;
③报废产品用黑牌标识;
④降等处理用合格证标识。
6.5 交付后不合格品的评审
6.5.1 交付后的产品发生不合格时,业务员在顾客单位进行确认,清点数量,办理有关手续。
6.5.2 退回的不合格品,库管员清点数量,办理有关退库手续,填写“产品退货统计表”一式两份,一份自留,一份上交质管部。
6.5.3 交付后的不合格品或退回的不合格品按6.4.2相关内容进行评审和标识。
6.6 评审过程中各部门对不合格的处置方式有分岐时,以质管部的意见处置不合
格品。
7.相关文件
7.1 检验、测试管理程序
7.2 仓储管理程序
7.3 生产管理程序
7.4 检验与测试状态识别程序
8.质量记录
8.1 原辅材料检验报告
8.2 过程检验记录
8.3 产品退货统计表
对不合格品(含原辅料)进行严格控制,防止不良品流出,确保出厂产品质量符合顾客要求。
2. 范围
适用于进货检验,生产全过程及出厂后发生的不合格品的控制。
3. 定义
为满足要求
4. 职责
4.1 各责任部门负责不合格品的隔离。
4.2 质检员负责不合格品的鉴别、标识。
4.3 质量部组织不合格品的评审。
4.4 生产部、销售部、市场研发部、设备部、生产工段参与不合格品的评审。
4.5 不合格品的发生部门按不合格品评审结果处置不合格品。
5. 不合格品控制程序流程图
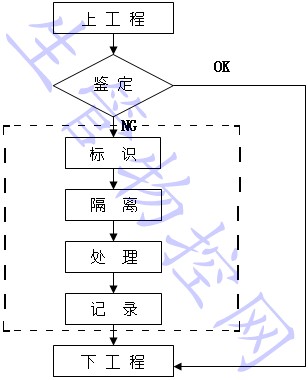
6. 内容及要求:
6.1 不合格品的分类
6.1.1 原辅材料的不合格品
6.1.2 工序产品的不合格品
6.1.2.1 正常消耗原因(试机、停机等原因)造成的不合格品
6.1.2.2 非正常消耗原因造成的不合格品
6.1.3 成品的不合格品
6.2 不合格品的确认
6.2.1 不能满足公司质量标准或顾客要求的产品均为不合格品。
6.2.2 操作人员负责自检过程不合格品的确认。
6.2.3 质检员负责检验和测试过程不合格品的确认。
6.2.4 业务员负责交付后不合格品的确认。#p#副标题#e#
6.3 不合格品的隔离
6.3.1 工序检验过程中出现的不合格品,由工段长和班长负责采取隔离措施。
6.3.2 最终检验不合格品应由质检员同跟班班长采取隔离措施,仓库、工段应提供不合格品放置区,以便不合格品能有效隔离。
6.3.3 原材料不合格品、出厂前检出的不合格品、顾客退回的不合格品、生产工段退回仓库的不合格品由库房采取隔离措施。
6.3.4 对于工序产品和成品出现的大批量的不合格品,质检员依照《检验和测试状态识别程序》对其标识及时上报质管部部长,以便及时处置。
6.4 原辅材料不合格品的评审、处置。
6.4.1 不合格品的评审、处置、标识。
6.4.1.1 原辅材料不合格品发生后12小时内,质管部、供应部必须对其进行评审,最晚不能超过24小时。
6.4.1.2 评审的原则:能否降等使用。
6.4.1.3 原辅材料不合格品的处置方式。
①降等接收;
②退货。
A.检验后拒收的原辅材料,由质管部部长确认后交供应部依据用料需求状况,以决议结果处理。
B.呆滞料判定未丧失主功能者,以退回分供方、折价出售或变更为其他用料,否则以报废处置。
6.4.1.4 质管部将处置结果记录在“原辅材料检验报告”的不合格品处置一栏中。
6.4.1.5 库管员依据“原辅材料检验报告”对处置后的不合格品进行标识。
6.4.1.6 原辅材料不合格品处置后的标识
A.降等接收的不合格品按区域分类码放,标明实际等级。
B.退货:隔离堆放,用“拒收标签”标识。
6.4.1.7 供应部负责与分供方联络退货的有关事宜,填写“退货记录”。
6.4.2 工序产品、成品的不合格品的评审、处置。
6.4.2.1 非正常消耗原因造成的不合格品,由工段主任、质检员、跟班班长现场处置,并在“过程检验记录”上记录。
6.4.2.2 非正常消耗原因造成的不合格品和成品的不合格品的评审。
①对偶然发生的且价值较小的单件或小批量的不合格品,直接由质检员处理,不再进行不合格的评审,但对处置结果必须在“过程检验记录”上记录。
②对价值较大的不合格品由责任部门以书面形式上报质管部,由质管部组织供应部、销售部、生产技术部、设备管理部、工段对不合格品进行评审;填写“不合格品评审处置报告”一式两份,质管部、生产技术部各一份;评审时间不能超过不合格品发生后24小时。#p#副标题#e#
6.4.2.3 评审内容
①不合格品产生的原因:
供应部从原辅材料的角度分析;生产技术部从技术的角度分析;设备管理部从设备的精度、完好程度分析;工段从操作的角度分析。
②不合格品的处置方式
6.4.2.4 不合格品处置方式的分类
①返工;
②返修;
③让步接收;
④报废:
⑤降等处理。
6.4.2.5 不合格品处置方式的标识
①返工、返修产品用紫牌标识;
②让步接收产品用蓝牌标识;
③报废产品用黑牌标识;
④降等处理用合格证标识。
6.5 交付后不合格品的评审
6.5.1 交付后的产品发生不合格时,业务员在顾客单位进行确认,清点数量,办理有关手续。
6.5.2 退回的不合格品,库管员清点数量,办理有关退库手续,填写“产品退货统计表”一式两份,一份自留,一份上交质管部。
6.5.3 交付后的不合格品或退回的不合格品按6.4.2相关内容进行评审和标识。
6.6 评审过程中各部门对不合格的处置方式有分岐时,以质管部的意见处置不合
格品。
7.相关文件
7.1 检验、测试管理程序
7.2 仓储管理程序
7.3 生产管理程序
7.4 检验与测试状态识别程序
8.质量记录
8.1 原辅材料检验报告
8.2 过程检验记录
8.3 产品退货统计表