开工准备与产品切换构成效率损失的解决办法
由于受到市场的影响,几乎每家工厂的生产订单都表现为单品种数量少、总量大、型号多、品种全。企业在制造产品的时候,往往进行频繁的产品切换和开工准备。而开工准备和产品切换一旦不到位,就会影响到企业生产效率的提升。那么我们该如何用快速换模法SMED来解决呢?
一、开工准备与产品切换的损失分析
1.开工准备与产品切换过程描述
在产品制造开工前,或者是新旧产品切换时,企业必须完成一些动作,从而避免因停机和等待造成的损失。这几个动作分别是:
(1)物料整备。
把老产品、没用完的原材料退回去,把新产品的原材料领过来。
(2)领取/理解/确认工艺要求。
领取、理解、确认相关新产品的工艺要求,包括作业指导书、工艺文件等。假如发现某工艺文件有问题,就需要与技术部门再次协商。
(3)工装模治具的装卸/清理/切换。
拆卸工装模治具,包括卸下老产品用的模具,装上新产品的模具;也包括很多工装以及部分车床可能更换的刀具;甚至包括对设备的装卸、清理和切换。
(4)工作教导(派活/顺活)。
一道工序应该由哪个员工来操作需要确认,这叫派活;一个员工应该做的工作,可能需要专门人员教,这叫顺活。
(5)设备的开机/暖机/调整/校正。
设备必须开机,某些设备开机时可能还需要暖机。又因设备可能产生很大的正负偏差,做出来的产品很可能有不合格的,所以还要对设备进行校正。
(6)产品的首件检查。
对设备进行校正后,需要进行试生产,直至第一个产品完全合格为止,开工准备或者产品切换的过程才算完成。
2.隐藏在流程中的效率黑洞
开工准备或者产品切换引起的效率损失,大约有90%跟工作流程有关。管理流程中,通常会隐藏着一些所谓的效率黑洞,即只有一部分流程是有价值的,其他的则是无价值的。具体情况如下图所示:
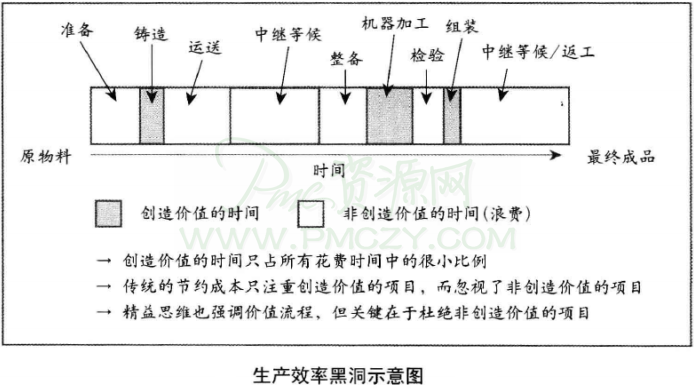
如上图所示,真正创造价值的只是深色部分,即铸造、机器加工和组装。而中间占绝大多数的白色部分,或许是必需的流程,但若能省略,即达到了提高效率的目的。
二、效率黑洞的消除改善分析
1.效率黑洞消除分析
从上图可知,提高效率的办法很简单:尽量消除效率黑洞的存在,即消除无价值的动作。如下图所示:
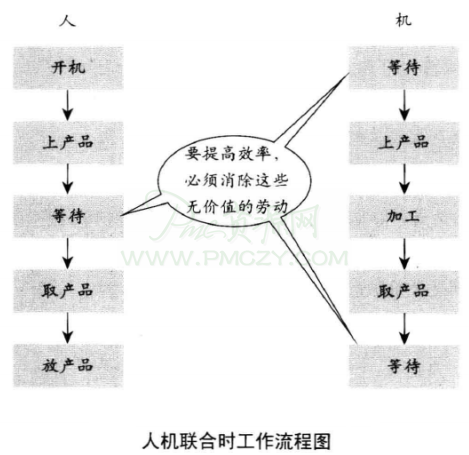
【案例】
丰田公司拥有畅流式的流水线。它把各种不同的设备按照生产一个产品的生产工序要求重新排列组合起来,每一个产品一道工序做完了,就马上交给下一道工序。依靠这种方式,丰田公司就能省略掉所有中间环节,比如中转的等待和搬运等等。当然就能缩短生产周期,使得开工准备和产品切换的损失也相应减少。
消除无价值的劳动是企业进行现场改善的最主要目标,但如何消除效率黑洞则是一个系统的工程。而日本丰田公司推出的快速换模法(即“SMED”)则是目前比较流行的黑洞效率消除办法。
2.快速换模法(SMED)
“快速换模法”是在9分钟以内把模具更换完成的方法,英文简称SMED。
这种方法是从日本丰田公司借鉴来的,它是变革流程改造的一个最典型的案例。如下图所示:
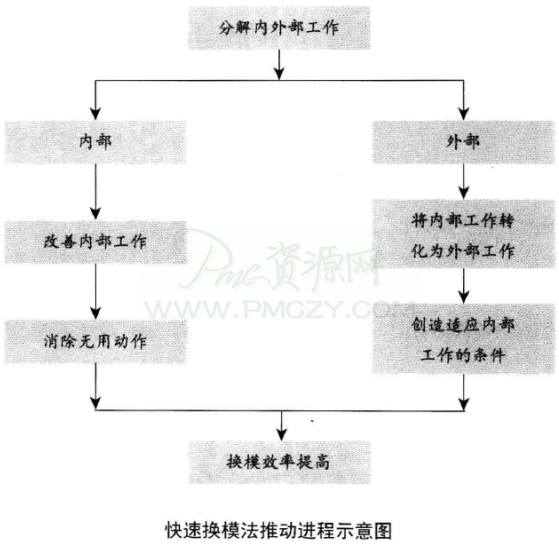
“快速换模法”是对换模过程进行优化,其具体过程如下:
第一步:分解换模的动作,将动作分为内部动作和外部动作。
①内部动作:机器停下来之后才能做的事情,叫内部动作。
②外部动作:在机器设备还没有停下来,机器还在生产原来的产品时,就可以提前做的事情叫外部动作。
第二步:依靠一些改变,能够把原来认定的内部动作变为外部动作。例如,塑料注塑,新的模具装上后,需要升温,升到一定温度以后,塑料才可以注进去。不然的话塑料注进去马上要卡模,因为它冷却快速,产品还没有成型就已经冷却。但为什么一定要将模具装上去之后才开始升温?日本很多搞注塑成型的企业简单地加了一套设备,使模具在外部升温,即机器设备还没有停下来时,就可以把新模具搬来升温了。这样,升温的时间很可能就从20分钟变成了5分钟。
第三步:想一些办法,压缩外部时间,寻找更快的工具和方法。比如平行操作、功能性夹具等。
开工准备、产品切换损失属于流程问题,可以用流程改造的方法改善。
就是说对整个工序重新进行排列组合,进行删除、合并、重组、简化之后,基本上就能把这种开工准备和产品切换的损失降到最小。
#p#副标题#e#
三、快速换模的五个步骤
快速切换的主要着眼点是减少切换、生产线停顿的时间,此种停顿时间越短越好。至于切换时耗用的人工时间是否能够减少,不是考虑的重点。当然如果切换的人工时间也能减少,那就最好不过了。
为了减少切换的时间,必须依据下列的思想步骤,循序渐进、按部就班来进行。
1.识别内部和外部活动
(1)定义。
内部活动是指必须在设备或操作停止后才能进行的动作,因而是浪费时间的动作;外部活动是设备在运行时也可以进行的动作。大多数准备动作都属于外部活动。而大多数替换、定位和调整都属于内部活动。
换模时间的缩短主要不是集中在总时间(外部时间+内部时间),而仅仅是在内部时间。当然,缩短整个换模时间也是必要的,但它只能居于次要地位。
换模过程包括:与换模人员进行讨论、对换模过程进行录像,并测量每一个步骤的时间等等。使用一个工作表记录换模过程并理解和描述整个过程。
在大多数工厂中,都没有对内部活动和外部活动进行区分,而是几乎把所有的活动都当做是内部活动。换模人员的动作基本上都是在设备停止状态下完成的,实际上根本没有必要这样做。
(2)运用的工具。
在这个过程中则需要充分运用以下工具:
①检查表。
对于每一个设备和工位,都要建立一个换模的参考检查表。这个检查表应当包含换模顺序、需要的零件、工具、夹具、物料以及产品规范等信息。在每一次进行换模时,换模人员都有安装检查表上的项目一项一项地进行操作,以便顺利地完成换模。②设备检验和维修。
应当定期检验设备的性能,并当作是外部换模活动。而这些活动也应当包含在检查表中。这样可以保证在换模期间机器不会出现异常。
③换模计划。
应当提前做好换模计划,这样就能在换模之前准备好需要的机器、工具、零件、物料及人员等。在拉动生产环境中,这种计划的换模可以根据看板来进行预测;在均衡生产中,每天的换模都是按照一定的规律重复进行的,所以很容易进行换模计划。
2.将内部活动转换为外部活动
改善换模过程最基本的原则是缩短内部时间。尽可能将以前在设备停止时(内部)进行的动作,在设备运行时(外部)完成。这就会使得内部时间大大缩短,通常是50%,但是还不能实现一分钟换模。然后就需要对所有的内部活动进行研究,看看能否再转换为外部时间。
3.缩短内部时间
要达到1分钟换模(小于10分钟),就需要优化内部活动。对于目前使用的设备进行改善,通常比购买新设备成本要低很多。使用标准化的工具对于标准化换模过程也是很有必要的。
应该对换模过程进行优化,使它不再成为批量生产的决定因素。也就是说可以实现多品种小批量生产。换模的经验法则是换模时间不要超过10分钟。新乡重夫的快速换模理念描述的换模方法非常简单,每一个作业员都能自己进行。这种换模过程的简化使得工厂不再依赖少数技术人员的熟练技能,可以根据客户的需求直接进行产品混合生产。
在该环节需要做好以下工作:
(1)换模动作并行。
同时进行多种换模动作可以大大缩短内部时间。有些情况下需要多个作业人员,有些情况下则不需要。然而,多个人员换模是一项团队任务,每一次换模时都要协调人员,因此可能会造成时间浪费。任何需要团队进行的换模,都要当做是临时的解决方案,尽量设法用一个人员来代替。
(2)设备安装。
当安装、固定模具到设备上时,通常会花费大量的时间。任何需要多于一个工具、多于一个人员或是多于一个动作的安装都是改善的目标。目前有很多有创意的设备都可以完成安装、固定的功能。螺栓是效率非常低的安装零件,最好能使用只需要一次就可以拧紧或松开的螺栓。对于固定零件实行标准化可以大大地缩短换模时间。因为这样就可以使用同一个工具,避免在寻找和拿取多个工具时浪费时间。
使用标准的容器、螺栓和夹具也可以令换模更加快捷,因为他们都是一次就可以安装到位的设备。
(3)消除调整。
大多数换模都会涉及一系列的调整动作,通常需要50%~70%的内部时间。在安装和模具调整之后,就是样品测试过程,即测量样品以及重新调整设备或模具。不管换模人员有多么熟练,都要经过这个过程。运行一测量一调整,会不断地重复循环,直到一切正常。这项工作通常是内部活动中最消耗时间的部分。
调整主要有以下三种类型:
①安装模具或是夹具到设备上。
②调整模具或夹具到正确的位置。
②调整模具或夹具到正确的位置。
③设定正确的速度、压力、进给速度、温度等等,以确定产出的零件满足要求。
由于机器上的污垢和油脂,机器、夹具和工具的尺寸、范围和标准都会有所变化。所以保持这些设备的清洁并经常校验,可以缩短摸索尝试的时间。
当只生产很少数量料号的零件时,可以在量具上标记常用的尺寸。
4.缩短外部时间
缩短外部时间对于缩短内部时间来说是次要的。因为最大的外部时间必须小于生产一个批量的时间,所以它一般不会成为换模的约束因素。然而,上面描述的工具也可以用于优化和标准化外部时间。
需要做好以下工作:
(1)储存。
换模需要的每一样东西(夹具、模具、工具、原材料和文件)应放到尽可能离换模地点比较近的地方,这样就能节约大量的外部时间。在一个机器旁频繁使用的东西,理论上必须放在机器旁边;使用不是很频繁的东西可以跟其他工位共享,但是应当放到中间位置。应该对储存进行合理安排,使得每一样东西都能很方便地找到。储存位置应用彩色标签进行标识,以便寻找,避免放错位置。
(2)换模工具箱和小车。
换模时往往需要用到夹具、工具和螺栓等。在大多数工厂中,这些东西都放在不同地点。换模时,换模人员必须走到几个不同的地点,找出他所需要的东西。有时候别人正在用,他还需要排队等候。
通过收集换模需要的工具,保存在特定的工具箱里,并放到离机器比较近的地方,往往可以大大减少走动、寻找、等待和挑拣工具的时间。这个工具箱也应当设计成影子面板的形式,避免工具放错位置或丢失。
当有的工具不能放到一个工具箱时,或是工具箱不能放到设备旁边时,也可以把工具或工具箱放到小车上。应当给每一个工具安排一个特定的位置,以便于放置和寻找。
(3)物料搬运。
应当安排适当的搬运设备用于换模的工具、夹具和物料的搬运。车间里的设备应当有合理的定位,以防止影响物料搬运设备的顺畅。应当对搬运设备进行定制或修改,以便于换模工具的搬运。例如,在顶上有滚轮的小车,具有合适的高度就可避免工具从小车滑到机器上;反之亦然。工具小车应该既便于放置新模具,也便于放置旧模具,从而便于换模,消除非增值动作。尽可能不要使用叉车和吊车,因为他们既占用空间,又不能专门用于换模。
5.重复以上步骤
完成了1~4步之后,就需要对整个换模过程标准化并设定防错措施。快速换模过程应该不断地使用,最终使换模能够在规定时间之内完成。
日本人新乡重夫提到了几种消除换模时间的方法:
(1)通过产品设计,尽可能使用通用的零件。
(2)一种模具尽可能生产更多的零件。
(3)一种设备专用于一种零件的生产(只推荐比较廉价的设备)。
(4)快速换模的目标是尽可能把换模的任务交给作业员,最小化非生产时间,最终消除换模。
#p#副标题#e#
四、换模技巧与法则
掌握了前述快速切换的思想步骤之后,所碰到的最大困难就是如何缩短机内作业、机外作业的动作时间。以下几个技巧及法则若能切实掌握,就能达到目的了。
1.平行操作
平行作业就是指两个人以上共同从事切换动作。平行作业最容易获得缩短机内作业时间的效果。如果一个人慢条斯理地从事切换动作,也许需耗1小时才能完成;但若能由两人共同作业,也许在40分钟或20分钟内就能完成。那么整个切换时间就由原先的1小时缩减为20~40分钟。而在平行作业中所需的人工时间或许会增多、不变、减少,这些都不是考虑的重点。因为,缩短了切换时间所获得的其他效果远大于人工成本的部分。而此点则是一般人较容易忽视的。在从事平行作业时,两人之间的配合动作必须演练熟练。尤需注意安全,不可因为疏忽而造成意外伤害。
2.双脚勿动
切换动作主要是依靠双手完成的,双脚必须减少移动或走动的机会。所以切换时使用到的道具、模具、清洁用具等,都必须放在专用的台车上,并且要有顺序地整理好,从而减少寻找的时间。模具或切换物品进出的路线,也必须设计成很容易进出的方式,并且切换的动作顺序要合理化、标准化。
3.特殊道具
工具就是一般用途的器具;道具则是为专门用途而特制的器具。就像魔术师表演时所用的扑克牌一样,都是经过特殊设计的。如果是一般的扑克牌,那么魔术师根本无法变出奇妙的魔术。所以魔术师所用的器具就称为道具,而不是工具。
切换时,应尽可能使用道具而不要使用工具。因为道具可提高切换的效率,从而缩短切换的时间。此外,测量的器具也要道具化,可以用块规或格条替代量尺或仪表来读取数值。最重要的一点就是设法减少道具的种类,以减少寻找、取放道具的时间。
4.剔除螺丝
切换时,螺丝是被用来固定模具最常见的方法。使用螺丝当然有其必要性,但是装卸螺丝的动作通常占去了很多的切换时间。如果仔细观察,还会发现,滥用螺丝的地方真是太多了。比如,本来只用四个螺丝就够了,却用了六个。这样拧螺丝的圈数太多,也耗费时间。而螺丝真正发挥上紧的功能,只有最后一圈而已。因此,改善的最佳对策就是消除使用螺丝的固定方式。比方说可用插销、压杆、中介夹具、卡式插座、轴式凸轮锁定、定位板等,来取代使用螺丝固定。
5.一转即定
限于某些状况,仍然必须使用螺栓、螺丝时,也要设法努力减少上紧及取下螺丝的时间。要以能做到不取下螺栓、螺丝而又能达到锁定的功能为改善的目标。其主要方法如下:
(1)可用只旋转一次即可拧紧或放松的方式。例如:C形开口垫圈,可垫在螺帽下,只需将螺帽旋松一圈之后,C形垫圈即可从开口处取下,达到完全放松的目的。上紧时反向行之,只需旋转一圈就可达到栓紧的目的。此外,如葫芦孔的方式也可达成此目的。
(2)就是使锁紧的部位高度固定化。过高的锁紧部位要削低至标准高度;过低的锁紧部位可加上垫块以达到标准的高度。每个模具锁紧部位的高度都标准化了之后,那么螺帽的上紧部位就随之固定了。如此可减少锁紧放松的旋转次数,当然也就减少了切换时间。
6.标准化
切换动作是因为产品不同而必须更换不同的模具或工作条件。因此也是必须作出调整的并需要设定新的标准的动作。切换动作通常需要花费整个切换时间的50%~70%,而且调整的时间长短差异很大。运气好时,一下子就调整好了;运气不好时,则需花费数十分钟,甚至数小时。
要排除调整的浪费,在方法上要掌握住标准不动的法则。换句话说,在机器上已经设定好的标准,不要因为更换模具,而又变动。具体做法如下:
(1)可把机内作业的调整动作移到机外作业,并事先做好设定的动作。
(2)不要拆卸整个模具,保留模座,只以更换模穴的母子式构造方式来消除模具的设定动作。
(3)可采用共用夹具的方式,以双组式的方式来做切换动作,即一组正在加工中,另外一组备材已经设定好了,切换时只需旋转过来即可立即达到切换的目的。
模具的高度标准化,也可以节省调整冲程的动作。又如射出成形机必须根据多使用的模具,调整设定数个不同冲程或条件,调整时可设定一个样板,套上去用手一拨即可全部同时设定好。最重要的是要取消以刻度式或仪表式读取数值的方式来认定工作条件,尽量改以块规等容易取放设定的方式来减少调整的时间,进而缩短切换时间。
7.事前准备
事前准备作业属于机外作业的一部分。机外作业如果做得不好,就会影响机内作业的顺利进行,从而使切换时间变长。
事前准备事项如下:
(1)设置换模专用车,将所需模具、道具、换模程序表及相关器材全部放在台车上,以减少个别寻找及搬运的时间。
(2)模具的摆放场所也要明确化,用有意义的编号方式来标示存放场所。
(3)器具、仪器、道具的储存不要以功能放置,而要以不同的产品或模具制作专用箱子放置,予以组套化较佳。
(4)设立查核表,协助检点所需器材是否齐全、编定标准切换程序表,并且区分作业,实施编组。
(5)平常的清洁、清扫、整理、整顿的动作也必须做好。