产品出入库管理办法
1、目的:
通过制定半成品、成品出入库管理办法及奖惩制度,指导和规范生产、检验、仓库工作人员日常作业行为,通过奖惩措施起到激励和考核人员的作用。
规范仓库管理,持续性改善仓库工作,确保仓库料账相符、先进先出。
强化统一管理、一致性作业,提高工作效率,减少沟通障碍。
2、依据:
依据本公司《生产作业管理程序》、《产品标识与追溯管理程序》、《不良品管理程序》和《仓储作业管理程序》,结合本公司生产、入库、发货的实际现状而制定本办法,规范生产入库、销货出库的流程。
3、适用范围:
本管理办法适用于本公司自制品的入库、出库及仓储作业,同时可做为原物料管理的参考办法。
4、权责:
4.1管理部:负责整个流程的推广,监督各部门的执行情况。
4.2生产部车间:负责产品的生产、包装与标识和生产入库单的开订。
4.3品质部:负责产品的检验,客户退货品的品质判定,以及库存品的检验、报废物料的判定。
4.4生产部仓库:负责入库产品的接收、保管,依据销售部的出货通知单进行备货、协助发货,打印送货单,并及时进行账目的更新。
4.5销售部:开立发货通知单给仓库;有大批量出货时,将出货情况提前告之仓库。
4.6司机:负责物料的运输,勤杂工装车卸货工作的安排。
5、产品出入库管理流程图:
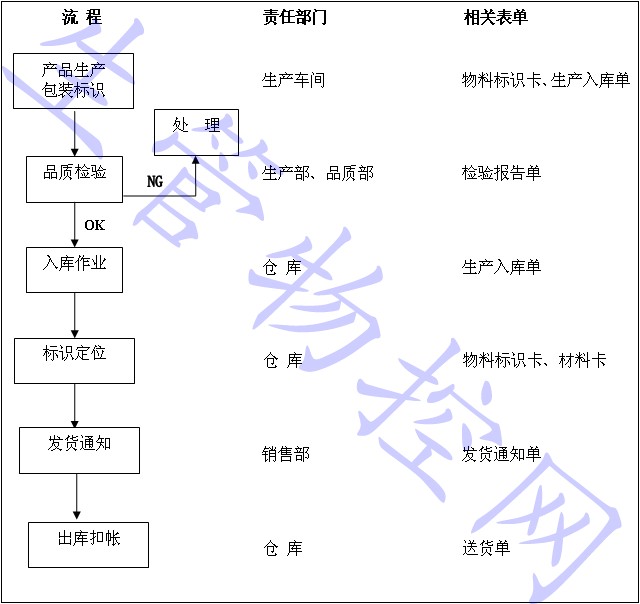
#p#副标题#e#
6、流程细则:
6.1产品的包装:生产员工必须按实际情况贴好物料标识卡(物料标识卡的备注栏上填上自已的姓名),合理的进行产品的码放。生产员工在包装产品前需要检查标识卡上数量、规格型号填写是否正确、并熟知包装要求和规范,根据生产任务单的要求对产品进行包装。 包装完成后的产品不要堆积过高过宽以防产品压坏和倾倒。
6.2产品交库:
6.2.1及时入库,每个班的产品要分开开单,不能混淆。由车间填写《生产入库单》,品检签字后交于入库人员,由入库人员与仓库库管员共同清点数量无误后签字确认;库管员指定入库人员将产品摆放合理之库位,并做好标识。物料摆放需要按照划分的区域进行摆放,不得随意摆放物料,不得在规划的区域外摆放物料,特殊情况需要在8小时内进行整理归位。
6.2.2如果产品直接从生产现场进行发货,则由发货的司机代替仓库签字,并备注“已发货”,然后将签字的“生产入库单”转交给仓库,做为仓库入库出库之依据,仓库打印“送货单”发货。
6.2.3如果产品需要修毛边,则由接收人员签收,并备注“需修毛边”,然后将签字的“生产入库单”转交给仓库,做为仓库入库出库之依据,仓库填写领料单发料。
6.2.4将“生产入库单”做为生产车间计件工作核算的唯一依据。
6.3产品的出库(成品发货):
6.3.1库管员根据业务发货通知单,清查库存,进行备货与发放。产品出库时要遵守先进先出的原则。
6.3.2备货时,若品缺货或短少,应将缺货情况告之仓库主管和业务员,并按实际发货情况打印送货单和扣账。
6.4销售退货:
6.4.1非本公司产品质量问题而退货的,库管员凭客户退货单重新办理入库手续, 并进行产品的入库。
6.4.2因公司产品质量问题客户提出退货时,经品质部核实属实的,库管员除进行账目更新外,还须按照公司的规定进行物料的报废处理。
6.5不良品的处理:
6.5.1对品质部判定的不良品,由仓库开立“物料报废单”,品质部签字后进行报废。
6.5.2不良品销毁后,库管员依据“物料报废单”进行出库扣账。
6.5.3库存产品发生破损,或在出库装卸时发生破损,或库存产品超过有效期,或受其它因素影响(如模具更改,客户产品变更)不能再销售,由库管员进行登记,定期填写“物料报废单”报领导批准后,对物料进行报废处理。
6.6物料的贮存保管:合理有效地利用库房空间,划分存放区域。库存产品应分类、分区存放,每批产品在明显的位置做出产品标识,防止错用、错发。具体要求如下:
● 库存产品标识包括产品名称、规格、入库日期,库管员需挂牌予以明示。
● 库存产品存放应做到“三齐”:堆放齐、码垛齐、排列齐。离地、离墙10~20厘米,并与屋顶保持一定距离;垛与垛之间应有适当间隔;
● 放置于货架上的产品,要按上轻下重的原则放置,以保持货架稳固。
6.7仓库内部管理
6.7.1仓库主管应对仓库进行不定期的抽查,检查账、物、卡相符状况,存放情况、标识情况,有无错放、混装及超期贮存、变质、损坏等现象。发现问题,及时解决。
6.7.2库管员应经常对库存产品进行检查和维护,发现变质、发霉或标识脱落等现象应及时向直接上级报告,及时处理。对有保质期的产品要防止失效。若超过保质期,应及时报验,并按《不良品管理程序》的规定处理。
6.7.3仓库人员应进行经常性动态盘点,做到日清日结,保持账、物、卡相符。
6.7.4仓库内严禁烟火,任何人都不得在仓库内吸烟。
6.7.5确实落实6S规划,对仓库经常性进行整理,清扫,保持良好的现场。
7.奖惩细则:
7.1生产员工不按要求对产品进行标识和码放的,怎么处罚
7.2生产员工所标识的数量与产品实际数量不符者,如何处罚
7.3“生产入库单”开单有误者,如何处罚
7.4发现以上情况有功者,如何奖励
7.5仓库抽盘发现料账不符超过3次者,如何处罚
7.6仓库6S工作到位,每个月抽盘料账相符,如何奖励。
8、参考文件:
8.1、《生产作业管理程序》
8.2、《仓储作业管理程序》
8.3、《不良品管理程序》
8.4、《产品标识与追溯管理程序》
9、使用表单
9.1《物料标识卡》
9.2《生产入库单》
9.3《送货单》
9.4《材料卡》
通过制定半成品、成品出入库管理办法及奖惩制度,指导和规范生产、检验、仓库工作人员日常作业行为,通过奖惩措施起到激励和考核人员的作用。
规范仓库管理,持续性改善仓库工作,确保仓库料账相符、先进先出。
强化统一管理、一致性作业,提高工作效率,减少沟通障碍。
2、依据:
依据本公司《生产作业管理程序》、《产品标识与追溯管理程序》、《不良品管理程序》和《仓储作业管理程序》,结合本公司生产、入库、发货的实际现状而制定本办法,规范生产入库、销货出库的流程。
3、适用范围:
本管理办法适用于本公司自制品的入库、出库及仓储作业,同时可做为原物料管理的参考办法。
4、权责:
4.1管理部:负责整个流程的推广,监督各部门的执行情况。
4.2生产部车间:负责产品的生产、包装与标识和生产入库单的开订。
4.3品质部:负责产品的检验,客户退货品的品质判定,以及库存品的检验、报废物料的判定。
4.4生产部仓库:负责入库产品的接收、保管,依据销售部的出货通知单进行备货、协助发货,打印送货单,并及时进行账目的更新。
4.5销售部:开立发货通知单给仓库;有大批量出货时,将出货情况提前告之仓库。
4.6司机:负责物料的运输,勤杂工装车卸货工作的安排。
5、产品出入库管理流程图:
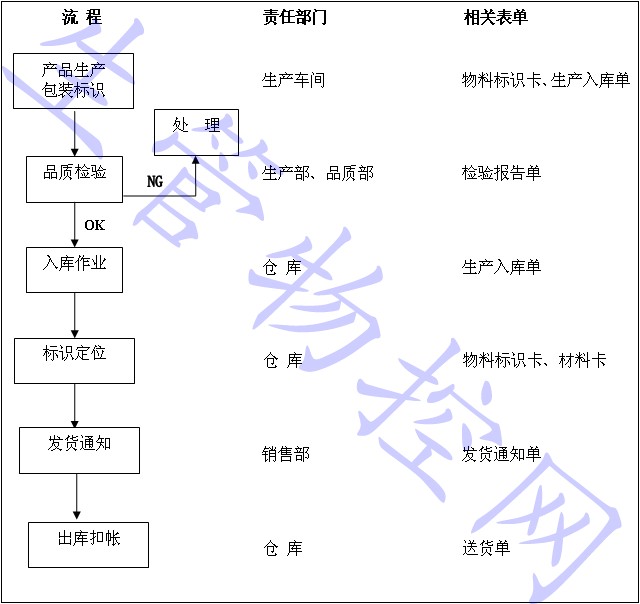
#p#副标题#e#
6、流程细则:
6.1产品的包装:生产员工必须按实际情况贴好物料标识卡(物料标识卡的备注栏上填上自已的姓名),合理的进行产品的码放。生产员工在包装产品前需要检查标识卡上数量、规格型号填写是否正确、并熟知包装要求和规范,根据生产任务单的要求对产品进行包装。 包装完成后的产品不要堆积过高过宽以防产品压坏和倾倒。
6.2产品交库:
6.2.1及时入库,每个班的产品要分开开单,不能混淆。由车间填写《生产入库单》,品检签字后交于入库人员,由入库人员与仓库库管员共同清点数量无误后签字确认;库管员指定入库人员将产品摆放合理之库位,并做好标识。物料摆放需要按照划分的区域进行摆放,不得随意摆放物料,不得在规划的区域外摆放物料,特殊情况需要在8小时内进行整理归位。
6.2.2如果产品直接从生产现场进行发货,则由发货的司机代替仓库签字,并备注“已发货”,然后将签字的“生产入库单”转交给仓库,做为仓库入库出库之依据,仓库打印“送货单”发货。
6.2.3如果产品需要修毛边,则由接收人员签收,并备注“需修毛边”,然后将签字的“生产入库单”转交给仓库,做为仓库入库出库之依据,仓库填写领料单发料。
6.2.4将“生产入库单”做为生产车间计件工作核算的唯一依据。
6.3产品的出库(成品发货):
6.3.1库管员根据业务发货通知单,清查库存,进行备货与发放。产品出库时要遵守先进先出的原则。
6.3.2备货时,若品缺货或短少,应将缺货情况告之仓库主管和业务员,并按实际发货情况打印送货单和扣账。
6.4销售退货:
6.4.1非本公司产品质量问题而退货的,库管员凭客户退货单重新办理入库手续, 并进行产品的入库。
6.4.2因公司产品质量问题客户提出退货时,经品质部核实属实的,库管员除进行账目更新外,还须按照公司的规定进行物料的报废处理。
6.5不良品的处理:
6.5.1对品质部判定的不良品,由仓库开立“物料报废单”,品质部签字后进行报废。
6.5.2不良品销毁后,库管员依据“物料报废单”进行出库扣账。
6.5.3库存产品发生破损,或在出库装卸时发生破损,或库存产品超过有效期,或受其它因素影响(如模具更改,客户产品变更)不能再销售,由库管员进行登记,定期填写“物料报废单”报领导批准后,对物料进行报废处理。
6.6物料的贮存保管:合理有效地利用库房空间,划分存放区域。库存产品应分类、分区存放,每批产品在明显的位置做出产品标识,防止错用、错发。具体要求如下:
● 库存产品标识包括产品名称、规格、入库日期,库管员需挂牌予以明示。
● 库存产品存放应做到“三齐”:堆放齐、码垛齐、排列齐。离地、离墙10~20厘米,并与屋顶保持一定距离;垛与垛之间应有适当间隔;
● 放置于货架上的产品,要按上轻下重的原则放置,以保持货架稳固。
6.7仓库内部管理
6.7.1仓库主管应对仓库进行不定期的抽查,检查账、物、卡相符状况,存放情况、标识情况,有无错放、混装及超期贮存、变质、损坏等现象。发现问题,及时解决。
6.7.2库管员应经常对库存产品进行检查和维护,发现变质、发霉或标识脱落等现象应及时向直接上级报告,及时处理。对有保质期的产品要防止失效。若超过保质期,应及时报验,并按《不良品管理程序》的规定处理。
6.7.3仓库人员应进行经常性动态盘点,做到日清日结,保持账、物、卡相符。
6.7.4仓库内严禁烟火,任何人都不得在仓库内吸烟。
6.7.5确实落实6S规划,对仓库经常性进行整理,清扫,保持良好的现场。
7.奖惩细则:
7.1生产员工不按要求对产品进行标识和码放的,怎么处罚
7.2生产员工所标识的数量与产品实际数量不符者,如何处罚
7.3“生产入库单”开单有误者,如何处罚
7.4发现以上情况有功者,如何奖励
7.5仓库抽盘发现料账不符超过3次者,如何处罚
7.6仓库6S工作到位,每个月抽盘料账相符,如何奖励。
8、参考文件:
8.1、《生产作业管理程序》
8.2、《仓储作业管理程序》
8.3、《不良品管理程序》
8.4、《产品标识与追溯管理程序》
9、使用表单
9.1《物料标识卡》
9.2《生产入库单》
9.3《送货单》
9.4《材料卡》