生产过程控制制度
1、目的
对影响生产质量的主要因素或环节实施控制,使生产过程、产品质量处于受控状态,确保生产出合格的产品。
2、适用范围
适用于公司产品装配、检验的工序质量的控制。
3、定义
3.1【过程】将输入转化为输出的一组彼此相关的资源和活动。
3.2【生产过程】由生产管理人员组织作业人员,按产品技术文件、工艺文件以及其它规定的要求,将原材料、半成品加工成产品的过程。
3.3【重要工序】本公司是指对产品质量形成过程有重要影响的,如老化前测试、成品测试等。
4、职责
4.1 生产部
4.1.1 生产部主管
a)策划并确定生产资源,组织、协调、指导生产部门人员照章生产;
b)协调部门内部以及与其它部门的关系,确保生产计划能保质保量完成。
4.1.2 班组长
a)按计划与有关技术文件组织生产;
b)指导、控制部门内生产活动,协调部门内部关系以及与他部门的关系;
c)工装、仪器设备的日常维护管理;
d)重点关注作业质量改善,及时反馈生产过程中的问题到相关部门,并协助处理;跟进物料上线使用情况并处理制程反馈物料问题。
4.2 PMC
4.2.1 按照市场预测、销售订单及生产能力情况,做出主生产计划。
4.2.2 半成品和成品的管理,原材料的的进、出管理以及库存的分析和控制。
4.3 工程部
4.3.1 协助生产流程安排,进行必要的现场操作指导和过程质量控制;
4.3.2 编制生产工艺指导文件;
4.3.7 负责检验、测量和试验设备的校验、维修和控制。
4.4 采购部
参与并执采购计划,对采购元器件的及时性、配套率和质量负责。
4.5 品质部
4.5.1 负责产品质量计划的制订及对生产过程中产品质量的监视和测量。
4.5.2 负责不合格品的处理、质量稽核及其质量状况统计分析。
4.5.3 编制生产质量标准,分析、解决生产过程中的质量问题。
4.5.4 按规定对生产物料、半成品、成品实施检验或试验,对验证和确认的产品质量负责;
5、程序
5.1 生产准备
5.1.1 相关部门接到《生产计划单》后,依计划表时程,进行人员、生产设备、工装夹具、检测设备及所有有关此产品的工艺技术、检验文件的准备。
5.1.2 物料员根据《生产计划单》和《领料单》到仓库领料。
5.1.3 在做生产准备同时,生产组长须事先对生产操作员工解说相关产品特性及质量控制要点,以利过程质量的控制。
5.2 首件生产
5.2.1 生产车间在每份生产工单生产开始前均须进行首件生产,生产数量以5个为宜。
5.2.2 生产首件后,生产车间提交IPQC确认。
5.2.3 如首检不合格,生产车间须通知相关技术人员、品管人员解决异常原因后,须重新生产首件交品管部门确认。
5.2.4 如因首检不合格而解决异常原因影响生产计划时,生产车间须通知生产计划部,由生产计划部作出生产调整。
5.3 批量生产
首件经品管部、工程部检验合格后,生产车间安排批量生产并根据《作业指导书》进行生产。
5.4 工序控制
5.4.1 员工能力
从事生产操作、检验的员工均须获得其工作范围所必要的能力,其能力培训的获得依《人力资源控制程序》进行。
5.4.2 设备的控制
设备的控制依《机器设备控制程序》进行。
5.4.3 物料的控制
5.4.3.1 各生产拉组需确保使用经检验合格或让步接收之物料进行生产,各物料均需有清晰的标识。
5.4.3.2 生产过程中发现的不合格物料(包括配件、原料、半成品),依《不合格品控制程序》进行处理。
5.4.3.3 生产用物料按车间规划的区域堆放,均须标明其状态。
5.4.4 生产方法
5.4.4.1 工程部、品质部、生产部须依规定职责范围制订技术文件、作业指导书、工艺流程图等,其内容包括工艺、图纸、检验规范和适宜的检测用具及设备等。
5.4.4.2 生产有关的作业指导书必要时须挂于相应的操作工位上,以利于操作员获得指导,操作员工必须按照作业指导书要求操作。
5.4.5 关键过程和特殊过程的控制
本公司的关键过程是各种产品的成品质量控制;特殊过程是电芯正负极点焊、保护板正负极点焊、半成品测试、自动及半自动包标机调试、成品测试。对这些过程应进行确认,证实它们的过程能力,适用时,这些确认的安排应包括:
a、过程鉴定,证实所使用的过程方法是否符合要求并有效实施;
b、对所使用的设备、设施能力(包括精确度、安全性、可用性等要求)及维护的严格要求,并保持维修保养记录,具体执行《机器设备控制程序》的有关规定;相关生产人员要进行岗位培训、考核,具体执行《人力资源控制程序》;
c、由技术人员确定合适工艺参数,工程部负责编制工序作业指导书,经工程部负责人审批后实施,以保证产品质量;
d、对这些过程的生产监控应进行记录,并保持这些记录;
e、过程的再确认:按规定的时间间隔或当生产条件发生变化时(如人员、物料、程序的变化等)应对上述过程进行再确认,确保影响过程能力的变化及时作出发应,根据需要对相应的生产工艺和作业指导书进行更改,执行《文件与资料控制程序》。#p#副标题#e#
5.5 过程检验
5.5.1 自检:各操作员工须对自己生产的产品作自检,防止不合格产品入库、发货和不良品转入下一工序。
5.5.2 互检:下工序员工对上工序的质量进行检验。
5.5.3 IPQC的检验控制依《过程检验控制程序》进行。
5.5.4 过程检验或生产过程中发现的不良品依《不合格品控制程序》进行处理。
5.6 经过程检验合格的产品,生产车间按客户要求进行包装。
5.7 各生产班组应日清日结,将实际生产情况做好《生产日报表》,供相关人员查阅。
5.8 品质部QC按《最终检验控制程序》进行检验。检验合格的成品,交拉长入库,检验不合格的成品依《不合格品控制程序》处理。
5.9 生产全过程中的产品标识依《产品标识和可追溯性控制程序》进行处理。
6、相关文件
6.1《机器设备控制程序》
6.2《不合格品控制程序》
6.3《作业指导书》
6.4《生产日报表》
7、本程序产生的质量记录
7.1 产品检验首件确认书
7.2 QC检测日报表
8、附件
生产过程控制流程图
对影响生产质量的主要因素或环节实施控制,使生产过程、产品质量处于受控状态,确保生产出合格的产品。
2、适用范围
适用于公司产品装配、检验的工序质量的控制。
3、定义
3.1【过程】将输入转化为输出的一组彼此相关的资源和活动。
3.2【生产过程】由生产管理人员组织作业人员,按产品技术文件、工艺文件以及其它规定的要求,将原材料、半成品加工成产品的过程。
3.3【重要工序】本公司是指对产品质量形成过程有重要影响的,如老化前测试、成品测试等。
4、职责
4.1 生产部
4.1.1 生产部主管
a)策划并确定生产资源,组织、协调、指导生产部门人员照章生产;
b)协调部门内部以及与其它部门的关系,确保生产计划能保质保量完成。
4.1.2 班组长
a)按计划与有关技术文件组织生产;
b)指导、控制部门内生产活动,协调部门内部关系以及与他部门的关系;
c)工装、仪器设备的日常维护管理;
d)重点关注作业质量改善,及时反馈生产过程中的问题到相关部门,并协助处理;跟进物料上线使用情况并处理制程反馈物料问题。
4.2 PMC
4.2.1 按照市场预测、销售订单及生产能力情况,做出主生产计划。
4.2.2 半成品和成品的管理,原材料的的进、出管理以及库存的分析和控制。
4.3 工程部
4.3.1 协助生产流程安排,进行必要的现场操作指导和过程质量控制;
4.3.2 编制生产工艺指导文件;
4.3.7 负责检验、测量和试验设备的校验、维修和控制。
4.4 采购部
参与并执采购计划,对采购元器件的及时性、配套率和质量负责。
4.5 品质部
4.5.1 负责产品质量计划的制订及对生产过程中产品质量的监视和测量。
4.5.2 负责不合格品的处理、质量稽核及其质量状况统计分析。
4.5.3 编制生产质量标准,分析、解决生产过程中的质量问题。
4.5.4 按规定对生产物料、半成品、成品实施检验或试验,对验证和确认的产品质量负责;
5、程序
5.1 生产准备
5.1.1 相关部门接到《生产计划单》后,依计划表时程,进行人员、生产设备、工装夹具、检测设备及所有有关此产品的工艺技术、检验文件的准备。
5.1.2 物料员根据《生产计划单》和《领料单》到仓库领料。
5.1.3 在做生产准备同时,生产组长须事先对生产操作员工解说相关产品特性及质量控制要点,以利过程质量的控制。
5.2 首件生产
5.2.1 生产车间在每份生产工单生产开始前均须进行首件生产,生产数量以5个为宜。
5.2.2 生产首件后,生产车间提交IPQC确认。
5.2.3 如首检不合格,生产车间须通知相关技术人员、品管人员解决异常原因后,须重新生产首件交品管部门确认。
5.2.4 如因首检不合格而解决异常原因影响生产计划时,生产车间须通知生产计划部,由生产计划部作出生产调整。
5.3 批量生产
首件经品管部、工程部检验合格后,生产车间安排批量生产并根据《作业指导书》进行生产。
5.4 工序控制
5.4.1 员工能力
从事生产操作、检验的员工均须获得其工作范围所必要的能力,其能力培训的获得依《人力资源控制程序》进行。
5.4.2 设备的控制
设备的控制依《机器设备控制程序》进行。
5.4.3 物料的控制
5.4.3.1 各生产拉组需确保使用经检验合格或让步接收之物料进行生产,各物料均需有清晰的标识。
5.4.3.2 生产过程中发现的不合格物料(包括配件、原料、半成品),依《不合格品控制程序》进行处理。
5.4.3.3 生产用物料按车间规划的区域堆放,均须标明其状态。
5.4.4 生产方法
5.4.4.1 工程部、品质部、生产部须依规定职责范围制订技术文件、作业指导书、工艺流程图等,其内容包括工艺、图纸、检验规范和适宜的检测用具及设备等。
5.4.4.2 生产有关的作业指导书必要时须挂于相应的操作工位上,以利于操作员获得指导,操作员工必须按照作业指导书要求操作。
5.4.5 关键过程和特殊过程的控制
本公司的关键过程是各种产品的成品质量控制;特殊过程是电芯正负极点焊、保护板正负极点焊、半成品测试、自动及半自动包标机调试、成品测试。对这些过程应进行确认,证实它们的过程能力,适用时,这些确认的安排应包括:
a、过程鉴定,证实所使用的过程方法是否符合要求并有效实施;
b、对所使用的设备、设施能力(包括精确度、安全性、可用性等要求)及维护的严格要求,并保持维修保养记录,具体执行《机器设备控制程序》的有关规定;相关生产人员要进行岗位培训、考核,具体执行《人力资源控制程序》;
c、由技术人员确定合适工艺参数,工程部负责编制工序作业指导书,经工程部负责人审批后实施,以保证产品质量;
d、对这些过程的生产监控应进行记录,并保持这些记录;
e、过程的再确认:按规定的时间间隔或当生产条件发生变化时(如人员、物料、程序的变化等)应对上述过程进行再确认,确保影响过程能力的变化及时作出发应,根据需要对相应的生产工艺和作业指导书进行更改,执行《文件与资料控制程序》。#p#副标题#e#
5.5 过程检验
5.5.1 自检:各操作员工须对自己生产的产品作自检,防止不合格产品入库、发货和不良品转入下一工序。
5.5.2 互检:下工序员工对上工序的质量进行检验。
5.5.3 IPQC的检验控制依《过程检验控制程序》进行。
5.5.4 过程检验或生产过程中发现的不良品依《不合格品控制程序》进行处理。
5.6 经过程检验合格的产品,生产车间按客户要求进行包装。
5.7 各生产班组应日清日结,将实际生产情况做好《生产日报表》,供相关人员查阅。
5.8 品质部QC按《最终检验控制程序》进行检验。检验合格的成品,交拉长入库,检验不合格的成品依《不合格品控制程序》处理。
5.9 生产全过程中的产品标识依《产品标识和可追溯性控制程序》进行处理。
6、相关文件
6.1《机器设备控制程序》
6.2《不合格品控制程序》
6.3《作业指导书》
6.4《生产日报表》
7、本程序产生的质量记录
7.1 产品检验首件确认书
7.2 QC检测日报表
8、附件
生产过程控制流程图
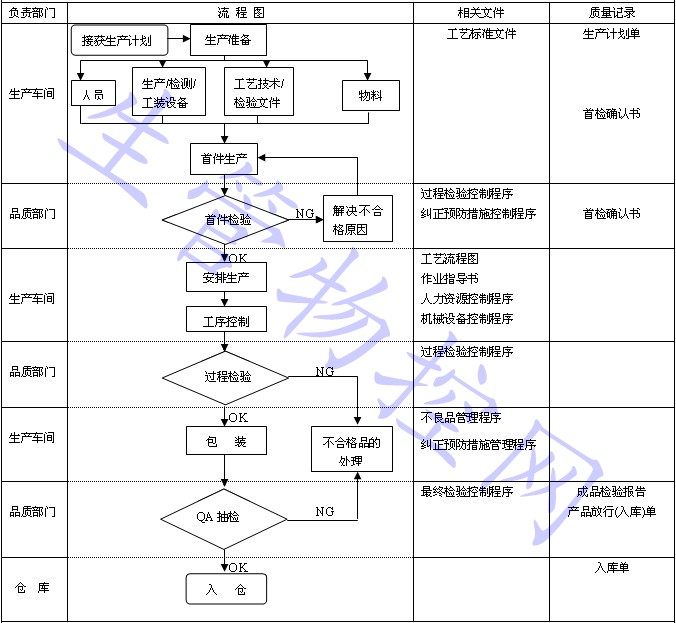