生产技术准备的主要环节和手段
在明确了生产技术准备工作的内容及任务的基础上,企业要加强生产技术准备管理。其主要环节和手段包括:采用先进的设计方法、寻求优化方案、重视技术改造和技术创新、缩短生产技术准备周期。
一、采用先进的设计方法
现代设计的方法很多,如计算机辅助设计、可靠性设计、维修性设计、模块化设计、优化设计、系统分析设计、相似理论设计等。采用现代设计方法,可以有效地改变传统设计中产品和工艺设计与生产设计相脱节的现象,从而提高产品制造的经济性,为优质、高效、低耗地从事生产活动打下良好基础。这里仅简单介绍几种设计方法。
1.计算机辅助设计(Computer Aided Design,简称CAD)。CAD是由设计人员根据市场需求、用户的具体需要提出构思,由计算机对有关产品的大量资料检索,根据性能要求及有关数据、公式进行计算和优化,将图形显示出来,然后由设计人员利用交互式图形显示系统对设计方案或图形做必要的修改,寻求出最优的方案或图形,将此结果以图形及数据形式加以输出。其中的主要工作由计算机来完成。
下图为计算机辅助设计的一般工作过程。
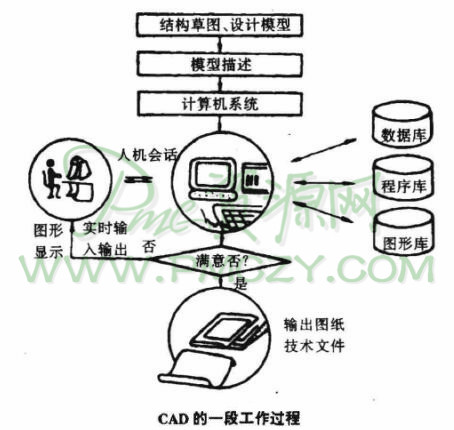
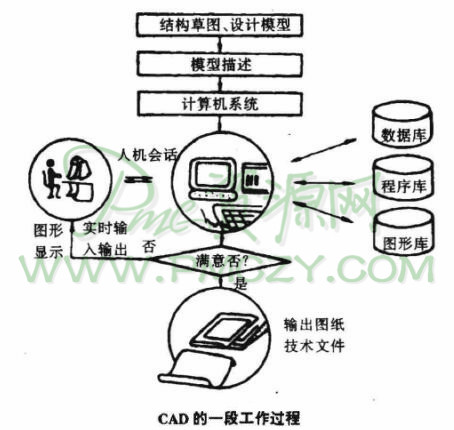
应用CAD必须具备以下条件:
①完整的数据库。凡与企业生产产品或开发产品有关的数据、资料、标准等应事先存入计算机的存储器中,以便在设计时调出使用,这些资料要随着时间的推移、工作的进展,不断地进行增加和删除。
②完备的程序库。使用CAD需将解决设计问题所需要的计算、分析方法,都编制成相应的计算机程序,汇集起来,以便设计时调出使用。
③具备人机会话功能的交互式图形系统。这种系统是指可以利用实时输入/输出装置,如光笔图形显示器、图像记录仪、自动绘图仪等,实时输出设计图纸及有关数据,实时输入设计人员的修改、调整指令等。
2.成组技术。成组技术又称群组技术,简称GT。它是以零件的相似性为基础,对零件进行分类编组,按组进行合理的生产技术准备和生产过程的组织和计划工作。成组技术之所以受重视。是因为它可以使多品种小批量生产得以成组组织生产,从而扩大批量,提高经济效益。
成组技术的主要工作内容如下:
①对企业所有零件,按几何形状、尺寸大小、加工工艺、精度要求、毛坯种类等进行相似性分析,并按一定的规则进行零件的分类编码,按照一定的相似性程度建立零件族、零件组。
②按照零件的分类编码,利用相似零件图册、设计指导资料来进行产品设计工作。这样,可以把相似性设计和标准化结合起来,尽量减少零件的种类和规格,从而增加零件结构和工艺的相似性,以便条件成熟时,建立零件设计准备自动化系统。
③按照成组工艺的要求改进工艺设计,制定零件族(组)的工艺方案和工艺规程,选择或设计制造成组加工设备、工艺装备,实现工艺要素和工艺装备的标准化。
在条件具备时,建立生产工艺准备自动化系统。
④根据企业生产大纲、设备数量与构成、零件族(组)的划分情况,建立成组生产单元和成组车间、制定投资规划、进行设备布置设计和工作地组织。
⑤按照成组工艺文件和成组生产单元来组织生产,相应制定和实施与成组技术有关的作业计划管理、劳动管理、经济核算的制度和方法。
从上述成组技术工作内容的叙述,可以清楚地看到它对产品设计的作用。应用成组技术进行产品设计,可通过企业中已设计、制造过的零件编码成组建立起的设计图纸和资料的检索系统中查找有关资料,将所设计的零件的结构形状、尺寸大小等转化成相应代码,然后按该代码对其所属零件组的零件设计图纸和资料进行检索,从中选择可直接采用或稍加修改便可采用的零件图纸。应用成组技术于产品设计的过程,见下图所示。
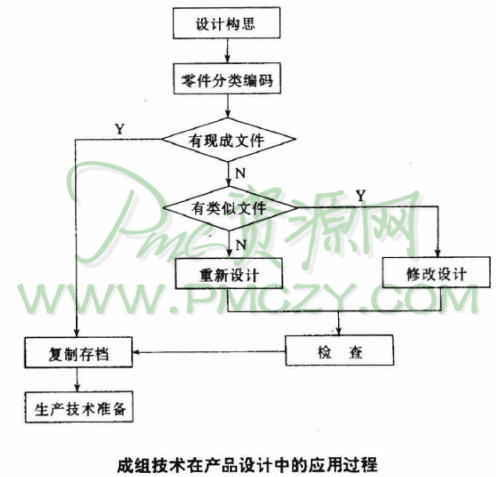
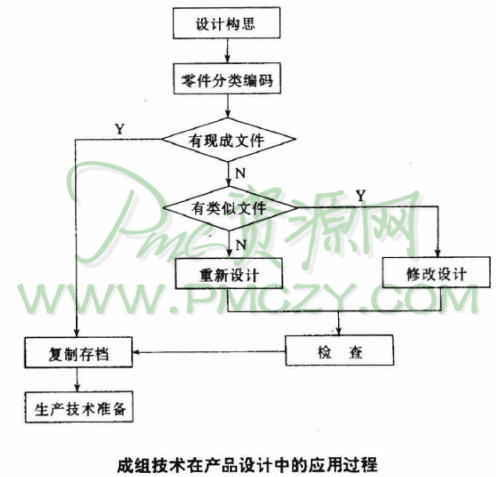
3.模块化设计。这种方法是以企业的标准件、通用件,以往生产过的零、部件为基础,以组合方式或以堆积木的形式来设计产品。在当今市场经济条件下,企业面临日益严峻的竞争,仅仅生产一种产品的企业是很难生存的。因此,大多数企业实行“哑铃式”战略,进行产品多样化生产,使产品设计强度加大。这里,模块化设计不失为一种敏捷式、低成本的设计方法。
4.内插式设计。它是一种介于原有两种产品规格之间的产品设计方法,是生产经验和实验研究相结合的设计方法,只要选对适当的相邻产品,用这种方法花费少,比较省力。
5.外推式设计。它是在现有产品的基础上,利用生产经验,将实践和技术知识外推,设计出新的产品。这种设计方法的工作量和工作难度较大,要有所创新,才能够提高产品的竞争力。
6.计算机辅助工艺过程设计。这是在工艺过程设计中使用计算机以提高设计的标准化、自动化的技术,是把产品的设计信息和企业的生产数据都输入计算机中,使系统产生出适用的工艺规程。从结构上看,计算机辅助工艺过程设计大体包括3种基本形式:
①检索式或称派生式。这种形式应用成组技术的原理,对现有零件进行编码、分类,按照工艺相似性组成不同的零件族(组),然后为每一族(组)编制一份族(组)内所有零件通用的标准工艺规程,将标准工艺规程存入计算机中。在编制新的零件工艺时,首先将新零件编码,依据编码找到它所归属的零件族(组)并检索出该零件族(组)对应的标准工艺规程,再由工艺设计人员按照该零件的设计要求对原标准工艺规程做必要的调整,就得到了该零件的工艺规程。这种方式开发起来比较容易、实用,但工作量大,创新性不够。
②创成式。创成式与检索式完全不同,是根据零件的几何、物理特征以及现在具备的生产工艺手段,综合技术性和综合性等因素,根据一系列的加工制造决策逻辑,自动从有关数据库中得到信息,在不需人工干预、调整的情况下,得出新零件的工艺规程。这是一种理想的方式,但困难很大,人们正在积极进行探索。
③混合式或半创成式,是对上述两种方式的折中。计算机根据零件的形状及加工要素等一系列原始设计信息进行逻辑判断,依据由已有零件分类归组之后总结出来的典型的优化工艺路线及典型的优化工艺手段编辑成一个新零件的工艺规程。它吸取了两种方式的优点,做起来又较容易。这种方式是目前进行计算机辅助工艺过程设计的主要形式。
③混合式或半创成式,是对上述两种方式的折中。计算机根据零件的形状及加工要素等一系列原始设计信息进行逻辑判断,依据由已有零件分类归组之后总结出来的典型的优化工艺路线及典型的优化工艺手段编辑成一个新零件的工艺规程。它吸取了两种方式的优点,做起来又较容易。这种方式是目前进行计算机辅助工艺过程设计的主要形式。
将计算机辅助设计、计算机辅助工艺过程设计、计算机辅助制造、计算机辅助工程,及计算机辅助生产管理等结合起来,能为计算机集成制造系统的实现创造良好的条件。
#p#副标题#e#
二、寻求优化方案
1.应用价值工程优化产品设计。价值工程(简称VE)是通过对研究对象的功能、成本分析,寻求用最经济的寿命周期费用实现产品必要功能的有组织的活动。
价值工程中所指的价值是功能与成本的比值,即这里的功能是指能满足用户需要的必要功能,成本是指用户为取得功能所支付的全部费用,包括购置费和使用费。衡量价值的大小主要是看功能(F)与成本(C)的比值如何。应用价值工程的目的是努力使产品物美价廉。价值工程的特征是:
①以功能分析为核心。功能分析是价值工程独有的研究方法。通过功能分析恰如其分地确定产品的必要功能,并寻求实现必要功能的最经济手段和方法。
②以不断创新为手段。价值工程的实质是“推陈出新”,否定原有的产品设计,打破原有的功能系统,综合运用各种创新技巧,改进老产品,开发新产品。
③以集团智慧为动力。运用价值工程改进和开发新产品时,要强调依靠集体的智慧,群策群力,集思广益,开发出更新的产品方案。
③以集团智慧为动力。运用价值工程改进和开发新产品时,要强调依靠集体的智慧,群策群力,集思广益,开发出更新的产品方案。
④以提高产品价值为目的。国外统计资料表明,在产品设计中,不必要的功能往往占30%左右,也就是说有30%的成本是耗用在不必要的功能上,造成了极大的浪费。而价值工程就是要消除这种浪费,通过功能分析,去掉多余、过剩及不必要的功能,从而降低产品成本,提高产品价值。
⑤以定量分析为根本方法。价值工程从确定对象开始,到功能评价、成本计量、新方案形成及实施,直至成果评价全过程的每一阶段都运用量化方法,将那些无法用统计、会计资料反映,不宜用具体尺度衡量的指标进行量化,从而使得对问题的论证,不再停留在“好、坏”的判断上,而是通过准确的量化进行比较和证明。应用价值工程的过程,实质上就是分析问题、发现问题和解决问题的过程。整个过程围绕8个基本问题展开:它是什么、它有什么用、它的成本是多少、它的价值是多少、是否有其他方法去实现此功能、新方案的成本是多少、新方案是否能满足要求、它的效果有多大。
从价值的表达式可以看出,提高价值的基本途径有:
①功能提高,成本降低;
①功能提高,成本降低;
②功能提高,成本不变;③功能不变,成本降低;④成本稍有提高,功能大大提高;
⑤功能稍有下降,成本大大下降。需注意的是,价值工程不是偷工减料。产品定价应在价值工程之后,不应在价值工程之前。
在产品设计阶段,使用价值工程意义很大,因为设计阶段在很大程度上决定了产品的性能和费用。一旦设计失误(成本高或功能不够),要么长时间地承受高成本和不适应市场需求的压力,要么付出返工的沉重代价。
(2)通过经济分析优化工艺方案。生产任何一种产品,在保证质量的前提下,往往可以采用不同的可供选择的工艺方案,这就产生了对工艺方案进行对比分析、选择最佳方案的问题。为此,要对不同的工艺方案作出经济评价,即对工艺方案进行经济分析,以便从中选择最优方案。这里,最常用的和最简便的选择方法就是工艺成本分析法。
采用工艺成本分析法,不需要分析全部产品成本的费用项目,只需分析与工艺过程直接有关的成本,并把它分为两部分:一部分是随产量变化而变化的变动成本;一部分是不随产量变化而变化的固定成本。年工艺总成本的计算公式如下:
C=VQ+F
式中:C一一年工艺总成本;
V一一单位可变费用;
Q——产量;
F——固定费用。
假设有两个工艺方案I和Ⅱ,方案I和Ⅱ的成本分别为
C1=V1Q+F1
C2=V1Q+F1
如果F1>F2,且V1>V2,则C1>C2,显然方案Ⅱ为优。如果F1>F2,而V1<V2,这时便可用工艺成本分析比较法进行分析。我们把两个方案的成本用图表示出来,见下图。
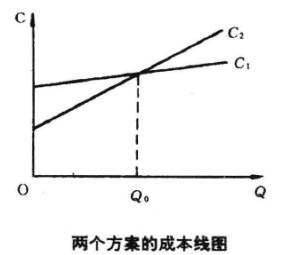
从上图中可以看出当年产量为Q。时,两个方案的年工艺总成本相等,这时C1=C2即
V1Qo+F1=V2Qo+F2得出
F1-F2
Q。=——————
V2-V1
Q。为临界产量。从上图中易见,当Q>Q。时,C1<C2,宜选择方案I;当Q<Q。时,则C1>C2,宜选择方案Ⅱ。因此,工艺成本分析法可以表述为:当产量大于临界产量时,宜选择固定费用高而可变费用低的工艺方案;当产量小于临界产量时,宜选择可变费用高而固定费用低的工艺方案。
#p#副标题#e#
三、重视技术改造和技术创新
“科学技术是第一生产力”,在生产技术准备环节中一定要重视技术改造和技术创新。只有如此,企业才能充满活力。
1.技术改造。技术改造是指在坚持科学技术进步的前提下,在企业现有的基础上,用先进的技术改造落后的技术,用先进的工艺和装备代替落后的工艺和装备,以改变落后的生产技术面貌,实现以内涵为主的扩大再生产,从而提高产品质量,促进产品更新换代,增加品种,适应市场需求,并节约能源,降低消耗,扩大生产规模,提高经济效益的活动。
从以外延为主扩大再生产转向以内涵为主扩大再生产,是实现两个转变的具体体现。技术改造的基本特征是内涵扩大再生产,它依托现有企业对原有技术、工艺、设备和产品进行更新和改造,这实质上是对现有资源进行重组和优化配置,因而具有投资少、见效快的特点。
技术改造有广义和狭义之分。广义的技术改造包括对企业进行全厂性、全面性的改造、改建和设备更新。狭义的技术改造,是指企业局部的设备更新改造、工艺改革、产品更新换代,厂房及生产性建筑物和公用工程的翻新、改造以及原材料的综合利用,“三废”的治理,零星固定资产的购置等。
技术改造是一项政策性、技术性、组织性很强的工作,应坚持如下原则:
①企业技术改造必须符合市场经济规律,围绕市场需求、产品需求来进行。
②企业技术改造必须以提高经济效益为目标,通过内涵扩大再生产,实现效益的增长。
③企业技术改造必须从我国国情出发。结合国家、企业的具体情况,充分利用国内现有资源,同时注意对国外先进技术的消化、吸收。
④企业技术改造要与企业的改革紧密结合在一起,应坚定不移地遵循“三改一加强”的方针,把技术改造与改革、改组和加强企业管理有机融合在一起,要把技术改造与正在进行的产业结构调整和企业产品结构调整结合好,发挥技术改造在其中的作用。
⑤企业技术改造必须坚持以技术进步为前提,要在企业积极开展科研活动,并尽快把科研成果转化为实际产品、工艺等,要积极地学习和吸收国内外先进技术。
⑥企业技术改造要统筹规划、分清主次、抓住重点,围绕对企业影响大的,抓一项能带动多项的项目进行。要量力而行,坚决不搞一哄而起、赶时髦的运动式活动,要扎扎实实、按部就班地进行,但要注意抓住机遇,不误时机。
⑦企业技术改造要坚持专群结合,充分发动和依靠群众,形成有觉悟、有技术、素质高的技术改造队伍。
技术改造项目的工作程序一般为三个阶段:
第一阶段:准备阶段,主要完成的工作有:
①提出并申报技术改造项目建议书;
①提出并申报技术改造项目建议书;
②编制和申报设计任务书或可行性研究报告或技术改造方案;
③在权力机构批准设计任务书、可行性研究报告或技术改造方案后进行初步设计的编制和申报,批准后列入年度计划。
③在权力机构批准设计任务书、可行性研究报告或技术改造方案后进行初步设计的编制和申报,批准后列入年度计划。
第二阶段:项目实施阶段,主要完成的工作有:
①按照年度计划组织施工;
②技术改造项目施工完成后,进行试生产运行,运行合格经验收、办理验收合格手续,正式交付使用。
①按照年度计划组织施工;
②技术改造项目施工完成后,进行试生产运行,运行合格经验收、办理验收合格手续,正式交付使用。
第三阶段:考核阶段,主要完成的工作有:
①竣工投产项目的效益跟踪;
②竣工投产项目的后评估,以便不断总结开展技术改造的经验教训,从而提高技术改造操作和管理水平。
①竣工投产项目的效益跟踪;
②竣工投产项目的后评估,以便不断总结开展技术改造的经验教训,从而提高技术改造操作和管理水平。
2.技术创新。技术创新是指一个从新产品或新工艺设想的产生到市场应用的完整过程。它是企业家把生产要求、生产条件、生产组织进行新的组合,建立高效的新的生产体系,生产新的产品,占领市场,获得良好效益的过程。技术创新包括新设想的产生、研究、开发、生产、实现商业化并进一步扩散等一系列活动。技术创新是科学技术和经济一体化的过程。它强调了技术创新的最终目的是技术商业应用和新产品进入市场成功。开展技术创新活动的经验表明,技术创新是实现科技进步、促进经济增长的根本源泉。
技术创新的基本内容包括:①产品创新;②工艺技术创新;③生产设备技术创新;④管理技术创新;⑤市场开辟的创新和资源创新等。
技术创新的特征是:①风险大;②投资大;③效益高;④动态开发性;⑤社会性。
四、缩短生产技术准备周期
目前,相当一部分企业由于生产技术准备周期过长而贻误了开发新产品的良机或失去了竞争优势,使企业蒙受巨大的损失。如何缩短生产技术准备周期,是企业所面临的一个至关重要的问题。就企业现有条件来看,除了加强统一领导和贯彻责任制外,在加速生产技术准备方面,可采取以下措施:
1.提高标准化水平,搞好工艺过程典型化和工艺装备规格化,可以大幅度节省生产技术准备工作量和缩短周期。
2.为企业各类产品制定一个先进合理的标准周期和定额,健全相关资料。
3.合理采用平行交叉作业。各技术准备部门的许多准备工作之间,如设计与工艺、工艺规程编制与工装设计,工装设计与工装制造,工装制造与试制工作,都可以组织平行交叉作业。
4.抓关键项目、压缩试制周期。在一般情况下,影响试制周期的是总的工序多、精度要求高的少数零件或部件。对产品的关键、主要零件和关键的工艺装备,可以在技术文件上标明。同时,要求设计部门尽可能把关键部件图纸优先发出,以便生产部门优先安排,提前投料,抓紧调度。
5.采用网络计划技术来编制生产技术准备计划表。这种方法适用于大型、复杂的新产品试制,对合理利用资源,缩短周期有显著效果。