APS(高级计划与排程系统)的结构
APS(高级计划与排程系统)能够使排程功能和规划功能相互协作。为了利用APS,就要事先构筑网罗了工厂生产能力和制约条件的模型。如果能够构筑良好的模型,就有可能制订反映实际生产状况并且能够发挥最大产能的小日程计划。
APS的模型构造如下图所示。制造产品需要经过一系列的工序步骤,而每道工序都有若干项作业。而且,进行作业时必须要有加工机械等生产资源。生产资源包括生产能力(是否包含作为替代的机械产能)和优先顺序(到达顺序、预定着手顺序、最小浮动时间顺序等)等诸多条件。另外,作业也包括作业时间和更换工序时间等。
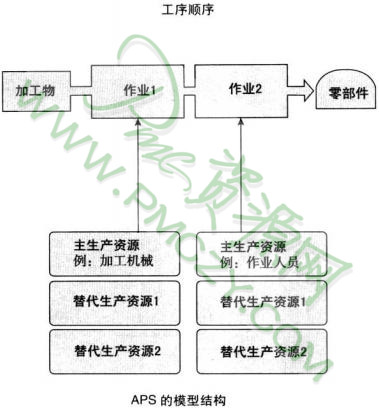
收集完这些条件之后就开始制作模型。模型不需要很精致,能够充分实现导人目的即可。
在MRP(物料需求计划)中使用的标准前置期,由各个工序的平均等待时间、平均工序转换时间构成。而在APS中,作业时间是按照不同的零部件单独计算的。
制订订单的需求量
作业时间 = ————————————— + 更换工序时间
分配的生产资源的处理能力
计算作业时间需必要合计生产资源的产能制约因素,因此要进行拆零计算。另外,当生产计划的变动或者是设备的故障等导致出现生产变动时,再次进行排程也要按照同样的步骤进行。
由于这些计算是采用运用了大容量主存储器的计算机进行的,因此能够快速制定可行性日程。
APS的模型构造如下图所示。制造产品需要经过一系列的工序步骤,而每道工序都有若干项作业。而且,进行作业时必须要有加工机械等生产资源。生产资源包括生产能力(是否包含作为替代的机械产能)和优先顺序(到达顺序、预定着手顺序、最小浮动时间顺序等)等诸多条件。另外,作业也包括作业时间和更换工序时间等。
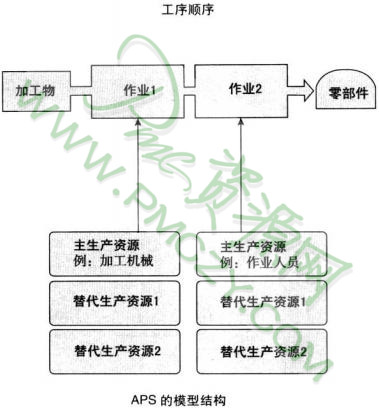
收集完这些条件之后就开始制作模型。模型不需要很精致,能够充分实现导人目的即可。
在MRP(物料需求计划)中使用的标准前置期,由各个工序的平均等待时间、平均工序转换时间构成。而在APS中,作业时间是按照不同的零部件单独计算的。
制订订单的需求量
作业时间 = ————————————— + 更换工序时间
分配的生产资源的处理能力
计算作业时间需必要合计生产资源的产能制约因素,因此要进行拆零计算。另外,当生产计划的变动或者是设备的故障等导致出现生产变动时,再次进行排程也要按照同样的步骤进行。
由于这些计算是采用运用了大容量主存储器的计算机进行的,因此能够快速制定可行性日程。