制程检验控制规定
1. 目的
规定生产过程中的检验和测试要求,确保只有合格品才能放行。
2. 适应范围
本规定适应于产品生产过程中的检验和测试活动。
3.职责
3.1 生产线各工位负责产品制程中的自主检查。
3.2 品管部QC负责制程产品的首检验证、巡检、抽检及测试活动。
3.3 生产部门负责及时对检验发现的不合格品进行处理。
4. 制程检验控制流程图
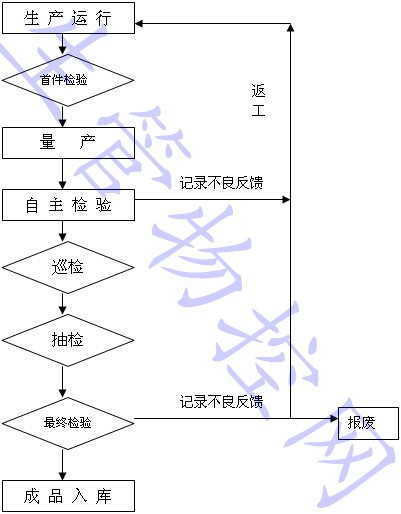
#p#副标题#e#
5. 制程检验规划
5.1 检验依据
5.1.1 每一型号产品投产时,QA工程师根据产品生产流程制定《QC工程表》,规定制程品质检验点、检查项目及检查方法等,作为制程品质检验依据。
5.1.2 研发部、工程部与品管部工程师分别为每一机型产品制定相应的测试及检验指导,规定产品检测内容及接收/拒收标准,作为制程QC的检验作业依据。
5.2 制程收件检验
5.2.1 对生产中规定实施收件检验的工序,各生产线应于每次生产开始或生产中换料、更换机型、工装模具、设备维修后实施收件检验。
注:装配线成品包装必须对前5台组装检验测试,具体为生产线负责前5台组装,品管部最终检验QC负责对其检验测试。
5.2.2 首检合格时,检查人员将合格首件标识单存,将首检三检交生产线,通知其产品可以批量生产;首检不合格时,检查人员通知生产线不合格现象,提出问题及可能的解决方案,并要求再次送样检查,如仍然不合格则应通知生产线班长、课长,必要时建议停产,直至问题解决,方可量产。
对装配线的前5台,检验如发现问题,立即通知生产线主管及QC主管,会同研发工程师及工程部工程师进行评审,问题解决后,重新送样,合格后量产。并做书面评审记录备查。
5.2.3 批量生产时,制程员工随时对自己上道工序作业状态进行自检和互检,以确保不使用不良品,不生产不良品,不流出不良品。
(1)制程员工自检发现产品出现误差或产品一致性不强等问题时,应立即停止生产,并报告现场QC及生产主管处理。
(2)装配线员工自检发现物料有明显缺陷或部件外观脏污、破损、声音异常或上道工序问题严重时,应及时报告跟线QC及生产主管。
5.4 制程巡回检查
5.4.1 生产线QC 依规定上午的检查频率及巡检路线依据图纸、检验知道书对制程物料、重要工艺参数及人员作业状况进行巡检及抽样检查,并对不合格品进行标识和记录,记录于检验记录表中:
(1)涂装课QC依规定的检查频率及巡检路线,依据图纸检验指导书和工厂订单,对制程的磷化质量、烘干温度、固化温度、链速、颜色/外观、涂层厚度进行巡检,并将巡检数据记录于喷涂检验记录表中,如发现异常,立即报告,QC主管及生产主管、现场主管必要时建议停产, 同5.2.2 如果出现问题必须彻底清查。
(2)装配课成品包装线最终检验QC,依据图纸、检验指导书、工厂订单、印刷品管控表对成品的外观、包装方式、印刷品、整机性能、安全性能全方位逐项检查测试,检查数据及不良点记录于成品检验报告,如摸中缺陷明显超出正常范围时,应发出停产要求,并要求生产线改善,每批产品的改动部分记录于成品检验报告书,以便于追溯,抽检数量按公司《单次抽检发》的规定执行。
6. 相关文件
6.1 《产品标识/可追溯性程序》
6.2 《不合格品控制程序》
6.3 《成品出货检验程序》
7. 记录表单
7.1 《首件三检单》
7.2 《检验记录表》
7.3 《成品出厂检验报告》
规定生产过程中的检验和测试要求,确保只有合格品才能放行。
2. 适应范围
本规定适应于产品生产过程中的检验和测试活动。
3.职责
3.1 生产线各工位负责产品制程中的自主检查。
3.2 品管部QC负责制程产品的首检验证、巡检、抽检及测试活动。
3.3 生产部门负责及时对检验发现的不合格品进行处理。
4. 制程检验控制流程图
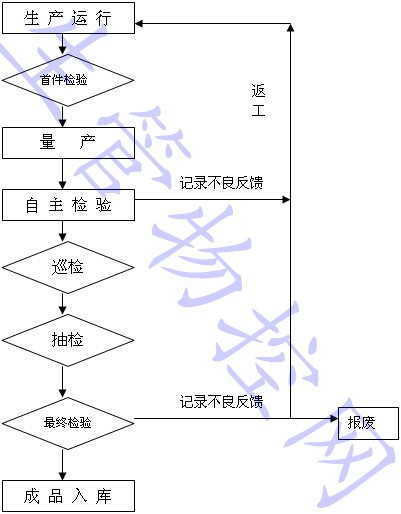
#p#副标题#e#
5. 制程检验规划
5.1 检验依据
5.1.1 每一型号产品投产时,QA工程师根据产品生产流程制定《QC工程表》,规定制程品质检验点、检查项目及检查方法等,作为制程品质检验依据。
5.1.2 研发部、工程部与品管部工程师分别为每一机型产品制定相应的测试及检验指导,规定产品检测内容及接收/拒收标准,作为制程QC的检验作业依据。
5.2 制程收件检验
5.2.1 对生产中规定实施收件检验的工序,各生产线应于每次生产开始或生产中换料、更换机型、工装模具、设备维修后实施收件检验。
注:装配线成品包装必须对前5台组装检验测试,具体为生产线负责前5台组装,品管部最终检验QC负责对其检验测试。
5.2.2 首检合格时,检查人员将合格首件标识单存,将首检三检交生产线,通知其产品可以批量生产;首检不合格时,检查人员通知生产线不合格现象,提出问题及可能的解决方案,并要求再次送样检查,如仍然不合格则应通知生产线班长、课长,必要时建议停产,直至问题解决,方可量产。
对装配线的前5台,检验如发现问题,立即通知生产线主管及QC主管,会同研发工程师及工程部工程师进行评审,问题解决后,重新送样,合格后量产。并做书面评审记录备查。
5.2.3 批量生产时,制程员工随时对自己上道工序作业状态进行自检和互检,以确保不使用不良品,不生产不良品,不流出不良品。
(1)制程员工自检发现产品出现误差或产品一致性不强等问题时,应立即停止生产,并报告现场QC及生产主管处理。
(2)装配线员工自检发现物料有明显缺陷或部件外观脏污、破损、声音异常或上道工序问题严重时,应及时报告跟线QC及生产主管。
5.4 制程巡回检查
5.4.1 生产线QC 依规定上午的检查频率及巡检路线依据图纸、检验知道书对制程物料、重要工艺参数及人员作业状况进行巡检及抽样检查,并对不合格品进行标识和记录,记录于检验记录表中:
(1)涂装课QC依规定的检查频率及巡检路线,依据图纸检验指导书和工厂订单,对制程的磷化质量、烘干温度、固化温度、链速、颜色/外观、涂层厚度进行巡检,并将巡检数据记录于喷涂检验记录表中,如发现异常,立即报告,QC主管及生产主管、现场主管必要时建议停产, 同5.2.2 如果出现问题必须彻底清查。
(2)装配课成品包装线最终检验QC,依据图纸、检验指导书、工厂订单、印刷品管控表对成品的外观、包装方式、印刷品、整机性能、安全性能全方位逐项检查测试,检查数据及不良点记录于成品检验报告,如摸中缺陷明显超出正常范围时,应发出停产要求,并要求生产线改善,每批产品的改动部分记录于成品检验报告书,以便于追溯,抽检数量按公司《单次抽检发》的规定执行。
6. 相关文件
6.1 《产品标识/可追溯性程序》
6.2 《不合格品控制程序》
6.3 《成品出货检验程序》
7. 记录表单
7.1 《首件三检单》
7.2 《检验记录表》
7.3 《成品出厂检验报告》