产品安全管制流程
1.0 目的
指导并预防生产过程中可能产生的安全差异,以及在产品出现安全异常后及时采取矫正处理措施,从而保证本公司生产的产品符合安全要求。
2.0 适用范围
适用于本公司。
3.0 权责
3.1 品保部:
3.1.1 安全材料检验,供货商稽核。
3.1.2 安全工序,安全测试设备及操作人员稽核。
3.1.3 安全成品检验。
3.1.4 安全测试报告,安规检查稽核,异常反馈、追踪、矫正措施验证。
3.2 研发部:
3.2.1 Safety报备,外来Safety文件管制。
3.2.2 制定各机种Safety Checking List。
3.2.3 供货商安规资料审核。
3.2.4 ENG Safety会签。
3.2.5 Safety Failure分析对策。
3.3 工程部:
3.3.1 仪器校验维修管制。
3.3.2 安全工序安排及标示编写。
3.3.3 安全工序操作员资格训练,鉴定.(PE)。
3.3.4 测试治具管制。
3.4 物控部:
3.4.1 Safety零件材料贮存,发放。
3.4.2 出货记录。
3.4.3 材料代用申请。
3.5 采购部:
3.5.1 提供厂商Safety证书及Safety零件材料样品。
3.5.2 新零件Safety报备申请。
4.0作业流程:
4.1 安全差异(Safety Discrepancy)
4.1.1 产品潜在的安全差异可能导致各种危险,而这些危险将直接或间接造成人身伤害或财产损失。
4.1.2 上述之各种"危险"包括: 电击、着火、辐射以及机械危险和热等危险。
4.2 安全差异之类型。
4.2.1 抗电强度.漏电流: 因零件、绝缘材料、 绝缘装置不符合Hi-pot试验技术条件要求使漏电流超出安全标准。
4.2.2 接地电阻及过载保护:零件、 材料、线路设计不符合相关安全要求。
4.2.3 安全材料:与安全相关之零组件及其它材料不符合有关安全要求。
4.2.4 安全标识:在产品零组件附件上缺少必要的安全提示、标志或有关提示标志内容不符合安全规定之要求。
4.2.5 安全工序:在制造过程中,对可能影响整机安全性能的有关工序没有按要求作业。
4.2.6 机械结构方面:
a.产品在机械上之稳定性差(无足够固定装置以防止摔倒)。
b.锐利棱角和其它可能可触及的零组件(包括附件)之尖锐机构物质。
c.无足够安全之包装防止装卸运送可能造成的损害。
d.不适当的开口(孔)或密封。
e.线材布置不当(如经过锐利物品边缘或高温物体表面或夹线等)。
4.3 安全零件、 材料
4.3.1 安全零件、材料之标识。
所有的与安全相关的零组件、材料应标示明确。
4.3.2 安规审核
a.Safety零件必须由RD安规工程师审核会签证实其符合safety要求和承认文件叙述的技术条件以及认证数据的相关规定,同时要求厂商提供safety认证报告,并对之审核。
b.依<<电子零件承认作业流程>>作业。#p#副标题#e#
4.3.3 零件/材料代用
a.零件/材料代用必须由物控开出零件代用申请单。
b.零件代用申请单必须经RD会签,涉及安规零件时,须由safety工程师验证并确认,满足safety要求和相关技术条件。
c.工程/品管单位主管须作审核会签。
4.3.4 ECN
所有牵涉safety零件之ECN必须由safety工程师签名认可。
4.3.5 Safety零件材料检验
a.IQC依<<进料检验作业流程>>作业。
b.发现safety材料异常时,必须依<<进料检验作业流程>>作业。
c.有关Safety材料检验及厂商送验报告必须保存3年以上。
4.4 安全相关工序管制
4.4.1 所有的安全相关工序之工位须由IE在该工位上用醒目之格式标明"SAFETY"或类似字样。
4.4.2 安全相关工站标识: PE、IE、PQC等部门间须交接明确。
4.4.3 安全相关工序之作业结果必须在随机卡相应制程记录栏目上作标示(签章)。
4.4.4 安全相关工序须由指定操作者作业,如果指定作业者离岗,该工站应由其它获得资格认证之操作员接替。
4.4.5 所有的安全工序操作者必须接受PE的资格培训,PQC对接受培训刚上线的操作者至少观察审核3天进行最终鉴定,所有的培训鉴定记录必须保存。
4.5.6 如果审核不合格或者作业中发生某些差异,须接受再培训。
a.上述审核不合格可以是PQC/IE/TE其中任何一单位审核之结果。
b.生产线/出货QA/客户反馈之差异,经审核不确实者。
4.5.7 接受再培训后仍出现差异者,则PQC和在线主管有权取消该操作员之资格,重新指定操作人员。
4.6 安全相关设备之校验。
4.6.1 耐压&接地测试仪器。
a.PQC对生产线相关仪器每日每班检查2次以上,并记录于耐压接地阻抗测试仪点检表上。
b.QE安规人员每日使用前必须自行校验。
4.6.2 所有安全相关设备之校验及每日自检与维修记录必须保存3年以上。
4.7 安全工序审核
4.7.1 IPQC必须对所有SAFETY工站进行稽核,并记录,确保每个工作日/每条线稽核2次以上。
4.7.2 测试工序之审核: IPQC检查仪器之设置使用是否符合要求&测试方法是否按作业指导书之步骤要求进行(稽核员每天审查二次)。
4.7.3 IPQC若发现生产线未落实点胶,立即通知QA HOLD所产出之成品,并要求生产部重工并经确认OK后,方可出货。
4.7.4 装配工具审核: IPQC检查电动或者气动批扭力维持要求的基本力矩(每周检查2次)。#p#副标题#e#
4.8 安全测试
4.8.1 QC对 Hi-pot、Grounding Test作100%测试并记录。
4.8.2 QA依照相关的作业准则之要求抽测。
4.8.3 IPQC稽核生产线若发现未落实执行测试,立即通知QA HOLD所产出之成品,并要求生产部重新测试后,方可出货。
4.8.4 测试记录于每月底由部门主管审核后交由品保部统一保存3年以上。
4.8.5 QE安规人员对Hi-pot、接地电阻抽样测试。
4.8.6 抽样比率: 正常状况0.1%,若生产线不同,机种不同,基板不同,Panel不同,班别不同则各抽一台。
4.9 矫正预防措施
4.9.1 当在生产中或在出货检验时发现产品有安全问题时:
a.生产线必须停止生产,同时PQC发出"安全异常通知单"知会相关部门分析处理,并签署 Failure Review Recor。
b.生产将不良产品提供给QE/PE/RD作初步分析,并将问题记录于Safety Failure Record。
c.PQC根据分析结果发出联络书,知会相关部门,由QA HOLD已做好的产品。
d.如果部分产品已出货,应通知客户截住这批产品等待进一步处理措施。
e.被HOLD之成品必须由QA/RD/ENG决定处理方式。
f.如果必须返工,RD、QE 、SAFETY工程师必须确认返工程序能有效地挑出问题,并且保证返工后能有效矫正不良。
g.安全问题之类型.原因.矫正措施以及在返工.修理之后的重新测试结果等必须记录归档。
4.9.2 当因安全测试设备故障,从上次功能检查到当次设备失效时所产出的产品必须重新测试。如产品己出厂,需招回此故障区间的产品后重新测试或以其它方式就地返工处理.
4.9.3 当因安全相关设备之校验问题导致问题时Safety Failure,PQC必须发出停线指令直到PE确认该问题处理OK为止。
4.10 附件表单记录保存期限为3年以上。
5.0 异常处理流程:
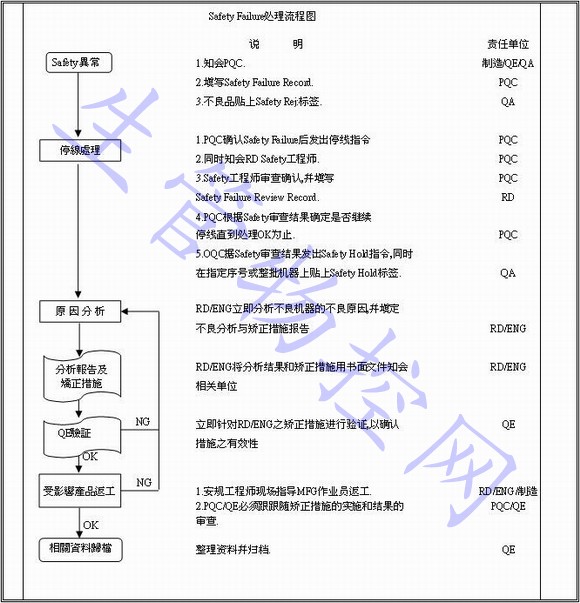
6.0 参考文件
6.1 《进料检验作业流程》
6.2 《矫正与预防措施作业流程》
6.3 《零件承认作业流程》
6.4 《不合格品控制作业流程》
7.0 表单附件
指导并预防生产过程中可能产生的安全差异,以及在产品出现安全异常后及时采取矫正处理措施,从而保证本公司生产的产品符合安全要求。
2.0 适用范围
适用于本公司。
3.0 权责
3.1 品保部:
3.1.1 安全材料检验,供货商稽核。
3.1.2 安全工序,安全测试设备及操作人员稽核。
3.1.3 安全成品检验。
3.1.4 安全测试报告,安规检查稽核,异常反馈、追踪、矫正措施验证。
3.2 研发部:
3.2.1 Safety报备,外来Safety文件管制。
3.2.2 制定各机种Safety Checking List。
3.2.3 供货商安规资料审核。
3.2.4 ENG Safety会签。
3.2.5 Safety Failure分析对策。
3.3 工程部:
3.3.1 仪器校验维修管制。
3.3.2 安全工序安排及标示编写。
3.3.3 安全工序操作员资格训练,鉴定.(PE)。
3.3.4 测试治具管制。
3.4 物控部:
3.4.1 Safety零件材料贮存,发放。
3.4.2 出货记录。
3.4.3 材料代用申请。
3.5 采购部:
3.5.1 提供厂商Safety证书及Safety零件材料样品。
3.5.2 新零件Safety报备申请。
4.0作业流程:
4.1 安全差异(Safety Discrepancy)
4.1.1 产品潜在的安全差异可能导致各种危险,而这些危险将直接或间接造成人身伤害或财产损失。
4.1.2 上述之各种"危险"包括: 电击、着火、辐射以及机械危险和热等危险。
4.2 安全差异之类型。
4.2.1 抗电强度.漏电流: 因零件、绝缘材料、 绝缘装置不符合Hi-pot试验技术条件要求使漏电流超出安全标准。
4.2.2 接地电阻及过载保护:零件、 材料、线路设计不符合相关安全要求。
4.2.3 安全材料:与安全相关之零组件及其它材料不符合有关安全要求。
4.2.4 安全标识:在产品零组件附件上缺少必要的安全提示、标志或有关提示标志内容不符合安全规定之要求。
4.2.5 安全工序:在制造过程中,对可能影响整机安全性能的有关工序没有按要求作业。
4.2.6 机械结构方面:
a.产品在机械上之稳定性差(无足够固定装置以防止摔倒)。
b.锐利棱角和其它可能可触及的零组件(包括附件)之尖锐机构物质。
c.无足够安全之包装防止装卸运送可能造成的损害。
d.不适当的开口(孔)或密封。
e.线材布置不当(如经过锐利物品边缘或高温物体表面或夹线等)。
4.3 安全零件、 材料
4.3.1 安全零件、材料之标识。
所有的与安全相关的零组件、材料应标示明确。
4.3.2 安规审核
a.Safety零件必须由RD安规工程师审核会签证实其符合safety要求和承认文件叙述的技术条件以及认证数据的相关规定,同时要求厂商提供safety认证报告,并对之审核。
b.依<<电子零件承认作业流程>>作业。#p#副标题#e#
4.3.3 零件/材料代用
a.零件/材料代用必须由物控开出零件代用申请单。
b.零件代用申请单必须经RD会签,涉及安规零件时,须由safety工程师验证并确认,满足safety要求和相关技术条件。
c.工程/品管单位主管须作审核会签。
4.3.4 ECN
所有牵涉safety零件之ECN必须由safety工程师签名认可。
4.3.5 Safety零件材料检验
a.IQC依<<进料检验作业流程>>作业。
b.发现safety材料异常时,必须依<<进料检验作业流程>>作业。
c.有关Safety材料检验及厂商送验报告必须保存3年以上。
4.4 安全相关工序管制
4.4.1 所有的安全相关工序之工位须由IE在该工位上用醒目之格式标明"SAFETY"或类似字样。
4.4.2 安全相关工站标识: PE、IE、PQC等部门间须交接明确。
4.4.3 安全相关工序之作业结果必须在随机卡相应制程记录栏目上作标示(签章)。
4.4.4 安全相关工序须由指定操作者作业,如果指定作业者离岗,该工站应由其它获得资格认证之操作员接替。
4.4.5 所有的安全工序操作者必须接受PE的资格培训,PQC对接受培训刚上线的操作者至少观察审核3天进行最终鉴定,所有的培训鉴定记录必须保存。
4.5.6 如果审核不合格或者作业中发生某些差异,须接受再培训。
a.上述审核不合格可以是PQC/IE/TE其中任何一单位审核之结果。
b.生产线/出货QA/客户反馈之差异,经审核不确实者。
4.5.7 接受再培训后仍出现差异者,则PQC和在线主管有权取消该操作员之资格,重新指定操作人员。
4.6 安全相关设备之校验。
4.6.1 耐压&接地测试仪器。
a.PQC对生产线相关仪器每日每班检查2次以上,并记录于耐压接地阻抗测试仪点检表上。
b.QE安规人员每日使用前必须自行校验。
4.6.2 所有安全相关设备之校验及每日自检与维修记录必须保存3年以上。
4.7 安全工序审核
4.7.1 IPQC必须对所有SAFETY工站进行稽核,并记录,确保每个工作日/每条线稽核2次以上。
4.7.2 测试工序之审核: IPQC检查仪器之设置使用是否符合要求&测试方法是否按作业指导书之步骤要求进行(稽核员每天审查二次)。
4.7.3 IPQC若发现生产线未落实点胶,立即通知QA HOLD所产出之成品,并要求生产部重工并经确认OK后,方可出货。
4.7.4 装配工具审核: IPQC检查电动或者气动批扭力维持要求的基本力矩(每周检查2次)。#p#副标题#e#
4.8 安全测试
4.8.1 QC对 Hi-pot、Grounding Test作100%测试并记录。
4.8.2 QA依照相关的作业准则之要求抽测。
4.8.3 IPQC稽核生产线若发现未落实执行测试,立即通知QA HOLD所产出之成品,并要求生产部重新测试后,方可出货。
4.8.4 测试记录于每月底由部门主管审核后交由品保部统一保存3年以上。
4.8.5 QE安规人员对Hi-pot、接地电阻抽样测试。
4.8.6 抽样比率: 正常状况0.1%,若生产线不同,机种不同,基板不同,Panel不同,班别不同则各抽一台。
4.9 矫正预防措施
4.9.1 当在生产中或在出货检验时发现产品有安全问题时:
a.生产线必须停止生产,同时PQC发出"安全异常通知单"知会相关部门分析处理,并签署 Failure Review Recor。
b.生产将不良产品提供给QE/PE/RD作初步分析,并将问题记录于Safety Failure Record。
c.PQC根据分析结果发出联络书,知会相关部门,由QA HOLD已做好的产品。
d.如果部分产品已出货,应通知客户截住这批产品等待进一步处理措施。
e.被HOLD之成品必须由QA/RD/ENG决定处理方式。
f.如果必须返工,RD、QE 、SAFETY工程师必须确认返工程序能有效地挑出问题,并且保证返工后能有效矫正不良。
g.安全问题之类型.原因.矫正措施以及在返工.修理之后的重新测试结果等必须记录归档。
4.9.2 当因安全测试设备故障,从上次功能检查到当次设备失效时所产出的产品必须重新测试。如产品己出厂,需招回此故障区间的产品后重新测试或以其它方式就地返工处理.
4.9.3 当因安全相关设备之校验问题导致问题时Safety Failure,PQC必须发出停线指令直到PE确认该问题处理OK为止。
4.10 附件表单记录保存期限为3年以上。
5.0 异常处理流程:
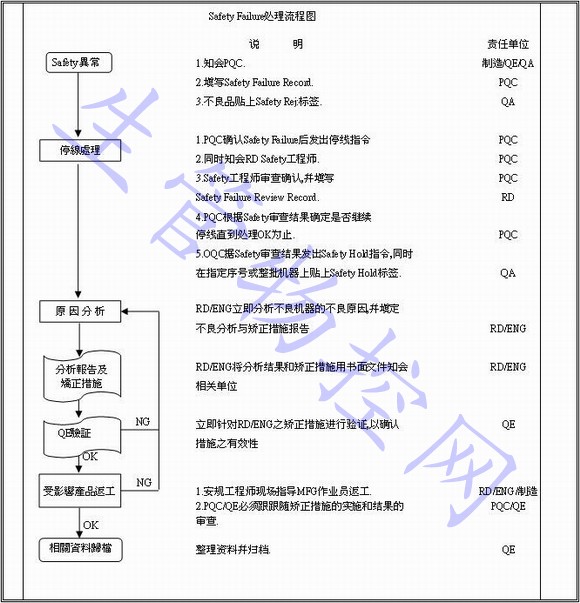
6.0 参考文件
6.1 《进料检验作业流程》
6.2 《矫正与预防措施作业流程》
6.3 《零件承认作业流程》
6.4 《不合格品控制作业流程》
7.0 表单附件