如何确定供应商审核的标准?
对供应商进行审核时,应确保公正客观,尽量避免主观因素对审核结果造成负面影响。这就要求审核人员按照事先制订好的审核标准,对供应商进行审核。
供应商审核标准是将对供应商审核时应注意的各要素加以量化的评审工具,它直接决定了供应商审核工作的质量。
一、确定供应商审核项目
制订供应商审核标准的首要工作就是确定供应商审核项目。供应商审核项目主要有品质系统、设计管制、原材料及供应商管理、制程控制、检验及测试、文件管制仪器校验、环境、不合格品的控制、持续改进、存储及支付、培训和客户服务13项内容。针对不同的供应商,审核标准的审核项目可作相应的增减。
二、依据审核项目分别制订评定标准审核项目确定之后,审核小组需要针对各个项目设定编号、评定分值和预设目标等,最重要的是要对各审核项目,设定具体的评分标准,如下表所示。
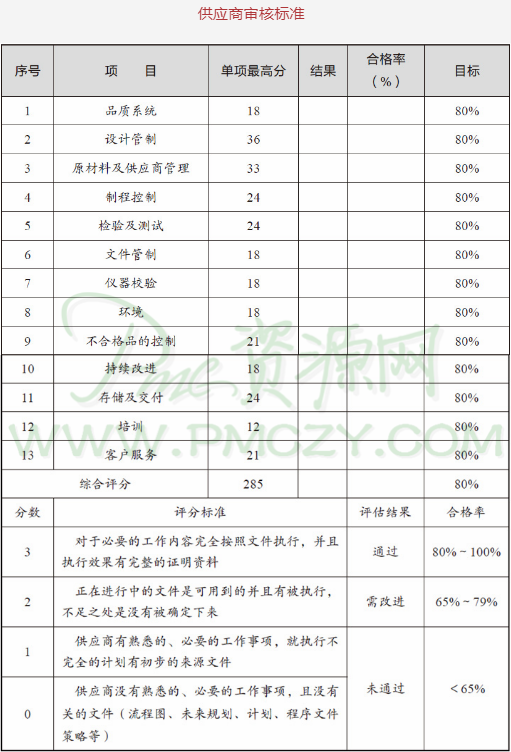
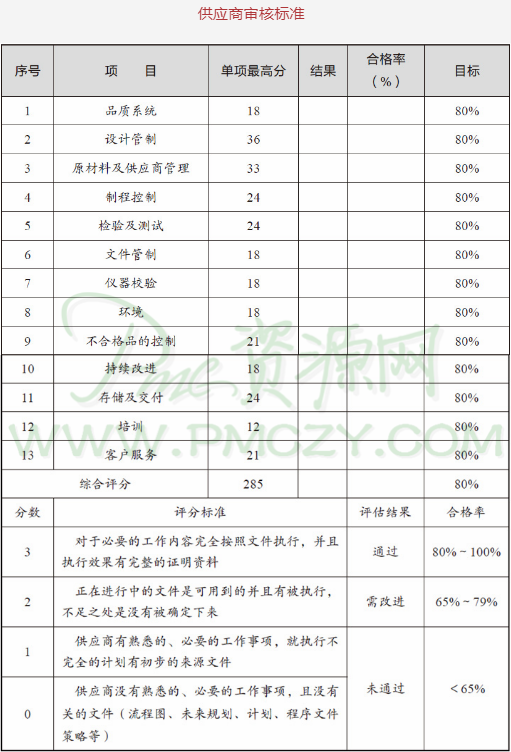
设定评分标准之后,审核小组还应对审核内容加以细分,并确定相应的评分点,供应商审核标准细分如下:
1.品质系统要求
1.1是否有明确的质量方针、质量目标?
1.2是否有文件确保品质政策被所有阶层了解并被拓展为部门目标而得以实施推行?
1.3|有无ISO或相关质量保证体系?
1.4质量目标及质量计划是否被持续改进?
1.5是否对从事品质管理、执行、验证的人员,明文规定其责任、授权与相互关系?
1.6是否定期进行内部审核,并有相应记录?
2.设计师管制
2.1是否有产品的设计流程来确保所设计的产品满足客户需求?
2.2设计阶段是否进行QFD(质量功能展开)和FMEA(失效模式和后果分析)?
2.3相关设计文件资料是否得到有效归档并受控?
2.4对设计开发的各阶段是否有明确的规划,并且经适当评审?
2.5在设计输入及变更中,客户要求是否得到有效体现?
2.6设计活动是否具备成本、性能、风险评估分析?
2.7设计变更是否得到评审、经过客户认可,并及时通知相关部门?
2.8是否在适当阶段针对设计结果进行审查,并留下书面记录?
2.9在设计过程中是否考虑了制程中的重要参数?
2.10对试生产及特殊产品有无明确的处理流程?
2.11对于所有设计开发过程中发现的问题,是否有及时反馈及纠正程序?效果如何?
2.12是否对产品进行了可靠性测试?是否留有记录?
3.原材料及供应商管理
3.1是否对新供应商实施了认证的机制,有没有严格实施?
3.2对现有供应商是否进行了定期考核,对不达标的供应商是否实施了推动改进或惩罚措施?
3.3针对供应商交期、品质或服务异常,是否有预防措施?
3.4对于供应商提供的新材料是否有品质确认程序?
3.5是否有进料检验规范的标准文件?
3.6是否对原材料的检验记录进行了保存,对保存期限有无明确规定?
3.7是否有检验设备或仪器能够检验来料的规格标准?
3.8检验设备或仪器是否定期维护、保养?是否有记录?
3.9不合格来料是否得到了有效处理?
3.10不合格物料的质量状况是否及时向供应商进行了通报并跟踪了供应商的改进措施?
4.制程控制
4.1是否根据产品及客户要求,设置了质量控制重点?
4.2对各质量控制点是否有明确的控制措施或标准?
4.3关键工序能力、重要参数及工艺操作要求是否得到确认并维持其有效性?
4.4制程异常问题是否得到了及时反馈及有效分析改进?
4.5是否对作业员作业有明确要求且要求被理解执行?
4.6现场质量状况是否被记录且可追溯?
4.7对关键工序是否进行统计过程控制(SPC)?
4.8是否有明确的操作程序(SOP)?有无受控?
5.检验及测试
5.1制程异常问题是否得到了及时反馈、分析,并采取了有效的预防措施?
5.2对于出货时的质量问题在制程上是否设有纠正预防措施?
5.3现场质量情况是否有记录且可追溯?
5.4对于最终产品是否有足够的检验文件、规范、规格书或抽样计划?
5.5最终验收的记录是否完善?
5.6是否进行周期性及可靠性测试?
5.7是否对成品测试失败进行了有效分析,并实施改善措施?
5.8出货时是否有完整的检验报告?
6.文件管制
6.1是否有设计开发文件、作业规范、作业标准及表单等文件?
6.2对所有制程文件及质量文件是否进行了有效管控?
6.3在发生质量问题后,是否可以追溯质量记录来追查原因?
6.4文件(记录)是否得到了有效的控制(审批、批准、发放、回收)?
6.5文件(记录)是否结构完整、内容清晰,便于理解?
6.6对于外部文件(包括客户提供的文件)是否进行了有效的管理?
7.仪器校验
7.1仪器校验人员是否具备作业认证合格证书?
7.2对仪器设备是否有明确的校正、保养、维护程序?
7.3是否有仪器清单和校正保养计划、实施计划,并留有记录?
7.4作业中使用的仪器是否适合并经过有效的校正保养?
7.5有特殊要求的仪器设备及工装是否有明确的管控要求并加以执行?
7.6生产、测试中有无未经校正的仪器使用?
8.环境
8.1是否有进行正式的5S活动、工作区是否整洁有序,且管理人员是否定期检查?
8.2生产现场是否区域划分明确、物流顺畅?
8.3生产现场是否有违规操作的行为?现场秩序如何?
8.4关键工序的温度、湿度、光照、通风等管控要求是否被明确执行?
8.5特殊物料或产品的存放、生产、搬运、包装的环境要求是否得到了满足?
8.6产品的质量状况是否在现场有明显标示,员工是否了解?
9.不合格品的控制
9.1是否有不合格品控制的程序文件?
9.2是否对退回的产品进行了分析、改进?有无反馈给各部门?
9.3是否有特定的人员和流程对不合格产品/物料进行处理?
9.4是否有对不合格品的处理办法?
9.5当对改进措施的推进或执行情况不满意时,是否采取了措施?
9.6改进措施是否包括长期的、根本的改善?
9.7是否有系统或流程跟踪改进措施的实施情况?
10.持续改进
10.1是否有持续改进的组织、流程?
10.2是否对重要的质量参数设定质量目标,并定期评审,进行持续改进?
10.3是否有推行质量持续改进的行动方案,以便研究内部产生不合格的原因,并采取改进的行动,防止再发生?
10.4是否制订了改进行动计划,及时处理客户关心的问题?
10.5改进的建议是否能被及时收集、分析、合理利用?有无文件规定?
10.6持续改进的经过、结果有无记录?效果如何?
11.存储与交付
11.1账、物、卡是否一致?
11.2是否执行了先进先出(FIFO)的原则?
11.3对超期及异常物料是否有明确的管制办法并严格执行?
11.4针对不良品、待判断品是否有明确的区域划分?
11.5库存产品是否堆放合理(限层,限高)?
11.6仓库各区域是否有明确划分?
11.7产品包装是否合理?
11.8是否有产品出货程序?
12.培训
12.1是否有培训体系,由专职培训人员保证员工接受持续培训或教育?
12.2员工入职是否进行岗位培训并有相应记录?
12.3关键岗位是否进行相应技能培训?
12.4工日常操作是否被记录,且针对其不足是否进行相应培训?
13.客户服务
13.1有无相关的流程对客户提出的要求进行回馈?效果如何?
13.2是否建立了相关机制,定期了解客户需求(如定期沟通)?
13.3客户提出的品质问题是否得到了及时有效的处理?
13.4是否有新产品的导入及首件流程?
13.5是否进行了客户的满意度调查,并有评价程序及标准?
13.6是否有“未经客户确认,不得改变原材料及重要制程”的程序要求?
13.7是否有能力发现不良并加以改善?
审核标准不是一成不变的,企业应根据实际情况以及外部环境的变化,不断修订并逐步完善供应商审核标准,使之更容易操作、更有实效性。